This post will address the processes and considerations surrounding version control of documents, management systems, and tips for how to get the most out of your document control system. You’ll learn about what document control is, and how it can be best applied to food manufacturing businesses.
As we dive into the topic, you’ll be interested to know that Food Industry Hub offers integrated management systems for food manufacturers, with a complete solution for version control, change management, and collation into the quality manual included as part of a holistic package.
Table of Contents
○ What Is Document Control?
○ Listing All Version-Controlled Documents and Indicating the Latest Version Numbers
○ Methods for Identification and Authorisation of Controlled Documents
○ Change Management and Documenting Amendments
○ Replacement of Superseded Versions of Updated Documents
○ Advantages of Digital Systems for Document Control
○ Potential Consequences for a Failure of Document Version Control
○ FAQ
○ In Summary
What Is Document Control?
Document version control refers to managing the revisions and updates made to documents in order to maintain accuracy and consistency. This process involves tracking changes, controlling access, and ensuring that only the live/active revision of a document is made available to use.
Document version control ensures that all stakeholders are working with the most up-to-date versions of documents such as standard operating procedures (SOPs), recipes, and equipment manuals. This helps to reduce the risk of errors, improve efficiency, and enhance overall product quality. Another benefit of document version control is increased collaboration among team members. By ensuring that everyone has access to the latest versions of documents at all times, it becomes easier for teams to work together on projects and collaborate effectively across different departments or locations. This can lead to faster turnaround times, better decision-making processes, and ultimately more successful outcomes for both businesses and consumers alike.
If you’re managing controlled documents manually (perhaps using an excel spreadsheet to track documents and versions, with the quality manual administrated separately from the version-controlled documents), the process of controlling documents can feel frustrating and heavily administrative. For this reason, document control might not be a topic that immediately inspires interest and passion across food professionals.
Despite the historically tedious nature of implementation, effective document control has an unsung importance for quality management. A food business might have the world’s best-developed and most robust quality manual in the world, but if it referred to inaccurate document revisions it would be haphazard at best, and actively damaging at worst.
○ As a manager, you want to be able to look at the current/active revision of a procedure and feel confident that that’s the revision of the procedure that’s being followed in the factory.
○ If you’re investigating a customer complaint, you want to be able to check which revision of a procedure was in effect on the production date for the product batch the complaint refers to.
○ If you update a production recipe, you want to be absolutely certain that production batches manufactured from the date of the change will be produced according to the revised recipe.
You can think about document control as the management system that all other management systems are built on. The effective implementation of procedures and work instructions for completely unrelated processes rely on document control.
The food safety and quality manual governs management interventions in the form of policies, procedures, briefing/training documents, reference documents, work instructions, risk assessments, signs/displays, or record sheets.
The document control system facilitates the existence of the food safety and quality manual by defining revisions of managerial documents referenced by the quality manual. Without this, it would not be feasible to implement complex management processes, so it’s illuminating to consider the underlying importance of document control – and the real managerial and operational benefits of getting it right.
Listing All Version-Controlled Documents and Indicating the Latest Version Numbers
Having an index of controlled documents, listed against their active revisions and revision details is -in many ways- the beneficial outcome yielded by a well-implemented document control system.
When you collate all policies, procedures, briefing/training documents, reference documents, work instructions, risk assessments, signs/displays, and record sheets into a centralised list.. that’s the food safety and quality manual. The culmination of management structures across the quality management system should be captured in a single register, which also identifies the current/active revision of each document.
Interestingly, the benefits to stakeholders offered by the quality manual are sequentially the reverse of the benefits that effective document control bring to management – in that the enquiry is “What document revision should I be referring to now?” across all documents, rather than “What revision was in effect when…” or “The change was introduced on…” for particular documents.
This is very significant, because delivering a food safety and quality manual – accurately composed of the correct versions of management documents -gives every employee working in the business confidence that they will be acting correctly if they refer to the systems, procedures, processes, and reference documents presented in the quality manual.
It can sound disingenuous when people talk about ‘building trust’ through management documents in this kind of setting… But at least consider the alternative. If people are skeptical about the reliability of the quality manual… If operators in the factory mix batches from memory without referring to the controlled recipes – that’s what a lack of trust looks like. You absolutely do not want to be in a situation where implementors throughout your food business lose faith in the integrity of the quality manual.
Systematically, to arrive at this food safety and quality manual and structure your quality management system, you’ve got to be able to identify documents, filter for activated/deactivated documents*, identify the active revision, and report that information into the document index.
*Documents may be deactivated and removed from the quality manual – irrespective of versions of those documents. For example, if an area of a production facility, the glass and brittle plastic register for that area might be deactivated and removed from the quality manual.
Maintaining the document index can be a point of vulnerability in the document control system as a result of the way these things are normally administrated. If a person has to update a document, and then update an excel spreadsheet to reflect the update, and then (where applicable) replace superseded copies, the fact that updating the document revision and updating the controlled document index are treated as two separate actions results in risk of data entry errors or omissions. The systems offered by Food Industry Hub automate the update to the quality manual with every new document revision, eliminating this potential for discrepancies.
No matter how you approach it, the controlled document index is incredibly important for quality management – you really can’t over-estimate this.
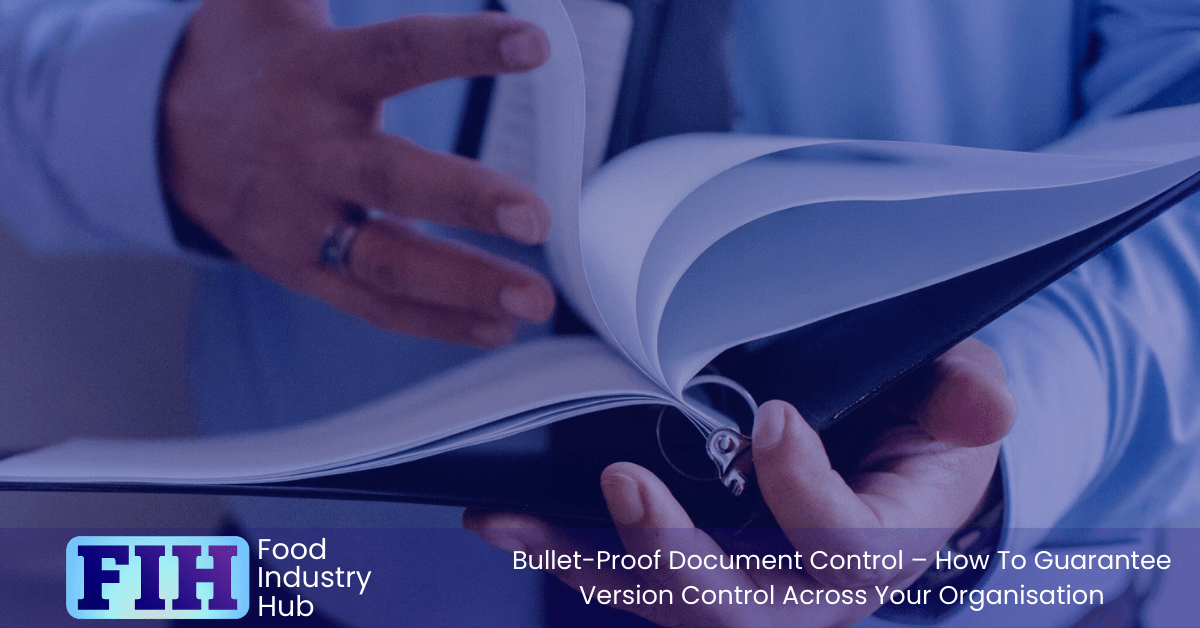
Methods for Identification and Authorisation of Controlled Documents
Every controlled document – and every revision of each controlled document – will have certain pieces of information associated with it.
As a point of interest, every website you visit – and every object you can see on webpages – have pieces of information associated with them. It’s called ‘metadata’ and this is information about something, whether or not that information is an observable attribute of the thing itself. You could think about the pieces of information associated with documents and revisions as being metadata about those documents and revisions.
The parameters associated with a document can be different to the parameters that would be applied to a revision of the same document. To illustrate…
Document parameters:
Document ID/reference
Document title
Status (Active/deactivated)
Revision history
Current/active revision
Date of introduction
Revision parameters:
Associated with [Document ID]
Revision number
Date controlled
Author [Person]
Reason for change
Authorised by [Person]
An effective document control system differentiates between document records and revision records – and reliably collects and processes that data in a way that facilitates references to documents and revisions. References to documents and revisions can be directed at the current/active revision, or at revisions in effect for a specified date range. A robust document control system also needs to be able to accommodate for enquiries about documents that were active for a given date range, but subsequentially deactivated.
The more you’re able to challenge and scrutinise documents and revisions, the more context information you have available to you for analysis and investigations into process deviations and nonconformities.
For compliance purposes, most criteria would be met just by having a list of documents along with their current revisions – which makes this a really great example of why systems should be oriented around management or operational advantage rather than just compliance. A document control system optimised only for compliance would yield a reference list – while a document control system optimised for functionality and practical use cases results in an accessible history of management structure as it has been applied to a facility.
Change Management and Documenting Amendments
Change management, in the context of document control, governs the process of proposing, reviewing, and approving changes to management documents. It provides a systematic approach to handle modifications and updates, ensuring that they are introduced smoothly, with minimal disruption, and in alignment with business operations.
You can think of this as a layer of management stacked on top of document control. Change management is the process that governs the transition of one document revision to the next. As a system, document control can exist independently of change management (i.e., it would be feasible to progress a document revision in the absence of a gated approval process). Conversely, change management could not be applied in the absence of version control – so it can be helpful to think of change management as subordinate to document version control.
Importance of Change Management in Document Control
Ensuring Accuracy and Compliance: Drawing on multiple individuals to challenge and criticise proposed changes to document revisions improves the likelihood of errors being identified, and presents an opportunity for different stakeholders to consider the adequacy and applicability of proposed document updates as they would be put into practice.
Engaging Stakeholders: By involving relevant stakeholders in the change management process, you tap into a wealth of knowledge and experience. More than that, though, the act of giving relevant stakeholders a say into the content of new revisions before they’re introduced is a very good move toward creating a situation where people voluntarily comply with systems because they’ve contributed to their development.
Risk Dilution: Food manufacturing inherently carries risks, from contamination concerns to quality control issues. Change management acts as a risk mitigation strategy by evaluating the potential impact of changes before they are implemented, reducing the likelihood of unintended consequences. Subjecting change proposals to challenge and criticism by a multi-disciplinary group can have a really positive impact by identifying potential risks which may not have been captured in the original change proposal, or by identifying unintended negative outcomes that may result from the introduction of the change.
Advantages of Implementing Change Management
Buy-In and Acceptance: Engaging employees and management in the change management process fosters a culture of buy-in and acceptance. When individuals understand the rationale behind changes and have a say in the decision-making, they are more likely to embrace and support the new procedures.
Employee Engagement: Involving employees in the change management process empowers them to contribute their insights and expertise. This not only enhances the quality of the changes but also boosts employee morale and engagement.
Risk Identification and Mitigation: Change management allows for a comprehensive assessment of potential risks associated with proposed changes. This proactive approach enables businesses to address vulnerabilities before they escalate into significant issues.
Enhanced Documentation: Change management ensures that every change is documented thoroughly, from the initial proposal to final implementation.
Effective Communication: Transparent communication is key to successful change management. Clearly communicating the reasons, benefits, and expected outcomes of changes cultivates a shared understanding and minimises confusion.
Sometimes, change management can feel like a bottleneck to document version control because numerous individuals need to review and feed back on proposed changes. This creates a temptation to bypass change management in favour of more streamlined updates to controlled documents.
To get the most out of change management, try not to think about it as something that slows the process of revision changes – think about it as a way to build engagement and create opportunities for improvement.
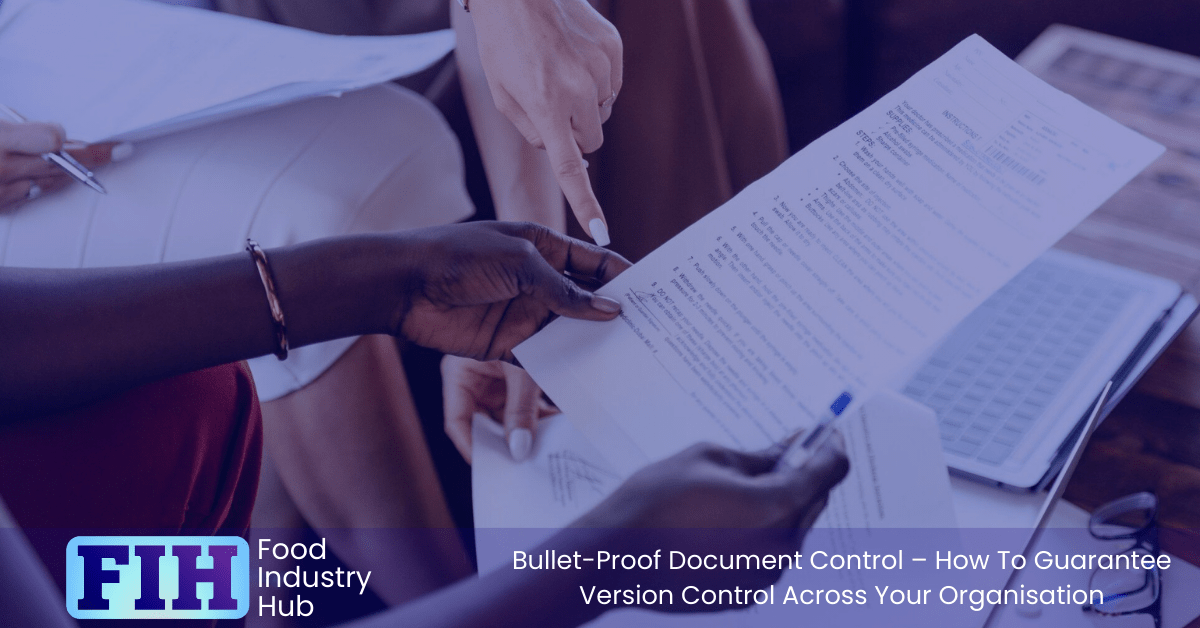
Sign-up for the Food Industry Hub Mail Service
We regularly produce new content for food industry professionals, and the Food Industry Hub Mail Service is the best way to stay up to date with the latest additions.
Signup today to be added to the Food Industry Hub mailing list.
Replacement of Superseded Versions of Updated Documents
Controlling and withdrawing superseded revisions is just as important to document control as activating new revisions.
If you introduce a new revision of a reference document, but the people who use the document are still referring to a printed copy of a superseded revision, it’s not just that the update was ineffective – you lose certainty over what revision was in effect for any date period. The document that’s ‘in effect’ is the one being used and influencing operational processes – regardless of what the controlled document index indicates.
The introduction of a new controlled revision of a document must have the effect of displacing the previous revision as the active copy.
Many documents are accessed electronically. The purchasing manager is likely to access the approved list for raw materials as an electronic copy, for example. Some documents, like recipes and record sheets*, are normally printed, resulting in physical copies of controlled documents.
*On record sheets, document control would apply to the document revision of the record sheet template, but not the content of a record. The content of a record sheet completed during operations would be governed by record completion and maintenance.
In practice, once a document revision is controlled and available to a wide group of people, it becomes very challenging to control every printed copy… That acknowledged, it’s predictable that certain documents will have printed copies, and when a new revision is introduced, particular care should be taken to collect and destroy and hard copies of superseded revisions. This will include signs/displays, certain reference documents (for example, acceptance criteria for consignments at goods intake), and process record sheets.
Advantages of Digital Systems for Document Control
In short, the overwhelming majority of challenges discussed here can be readily overcome with digitisation.
The systems offered by Food Industry Hub deliver a document control system as one feature among many included in a holistic package. The controlled documents module enables you to administrate documents and their revisions – along with incorporating change management.
Updating a new revision has the instant effect of updating the quality manual with the new active revision and reason for change.
Individual users can be given access permission to add and edit controlled documents, or access the current/active revision of documents included in the quality manual, or both.
By making all documents centrally accessible (while restricting the users able to make changes), changes can be introduced at the click of a button – with all users provided with the new active revision instantaneously.
Similarly, providing all users with access to the current revision of every controlled document removes incentives for people to retain uncontrolled copies of documents – because they’ll have the assurance of knowing they’ll have access to the documents they need.
Many offline approaches to document control and the delivery of the quality manual suffer from a detachment of the management structure as it is documented and the management interaction that employees are engaged with. The classic example is the quality manual, printed and arranged in folders in the office; far removed from the operatives in the factory.
A really key advantage of making the systematically accurate quality manual available to everyone in your business is that people who are interested (and given the opportunity) will read it.
Development of food safety and quality culture, and workforce engagement – these things are being discussed as new and novel concepts, with improvement initiatives largely focussed on behaviours. Another way of thinking about this would be that proactively making the current revision of every document in the quality manual easily accessible to every employee could actually have a substantive effect on engagement.
Potential Consequences for a Failure of Document Version Control
Failure to enforce proper document version control can have severe consequences for the food manufacturing business. Inaccurate or outdated documentation can lead to costly mistakes and even pose a risk to public health.
For example, if a recipe is updated but the incorrect version of the instructions is followed, it could result in an inconsistent product that fails to meet quality standards or even worse, poses a health risk to consumers. Similarly, if changes are made to important policies or procedures without proper version control, employees may not be aware of these changes and could make critical errors.
Think about the consequences for consumer safety if critical systems such as the HACCP plan were subject to failures in document control.
In addition to these risks, there are also compliance implications for failing to maintain accurate document version control. Quality assurance schemes universally require strict documentation practices for food manufacturers in order to ensure compliance with safety regulations. Failure to comply with these regulations can result in fines or other penalties that can greatly impact the business’s bottom line. Overall, maintaining effective document version control is essential for ensuring consistent quality and safety within the food manufacturing industry while also mitigating financial and legal risks associated with non-compliance.
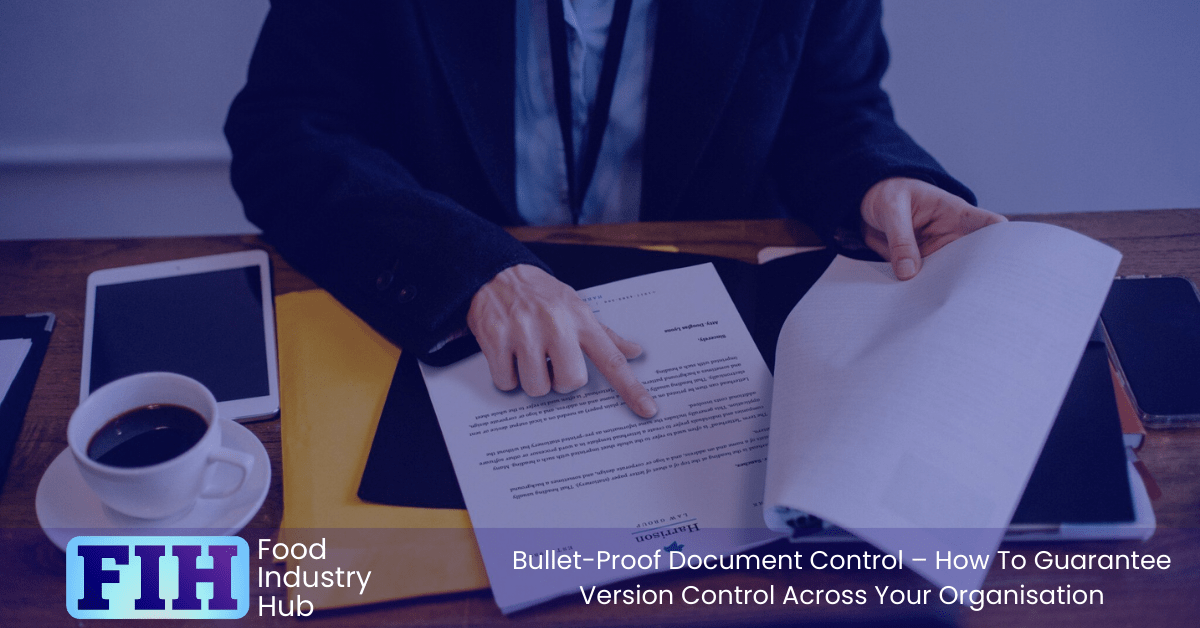
FAQ
Why is document control important for food manufacturers?
Food Safety and Quality: The top priority for any food manufacturer is ensuring the safety and quality of their products. Document control ensures that accurate and up-to-date procedures are followed, minimising the risk of deviation from documented manufacturing instructions and management structures.
Compliance: The food industry is heavily regulated to protect consumers from health risks and ensure product authenticity. Document control is a core requirement of all major assurance schemes – so regardless of regulatory interventions, document control is a mandatory requirement for most food manufacturers.
Consistency and Standardisation: Document control establishes consistent processes and practices across all aspects of food manufacturing. This uniformity ensures that products are produced with the same specifications and characteristics, regardless of shifts or personnel changes. The culmination of the food safety and quality manual (facilitated by effective document control) should be permissive of repeatable and scalable processes that food businesses employ for consistent operation. Document control is the foundation for this managerial structure.
Operational Efficiency: Well-documented and standardised procedures streamline operations by providing employees with clear instructions. Document control reduces confusion, minimises downtime, and improves overall efficiency across a range of manufacturing processes and surrounding operations.
New Employee Onboarding and Training: Document control ensures that new employees are trained with the most current procedures and guidelines. This accelerates the onboarding process and contributes to a skilled workforce capable of adhering to established practices.
In summary, document control is the linchpin that ensures the safe, efficient, and compliant production of food products. By meticulously managing documents and procedures, food manufacturers can uphold the highest standards of quality and safety, mitigate risks, and build trust with consumers, regulatory bodies, and stakeholders. Effective document control is an essential investment that directly contributes to the success, reputation, and growth of food manufacturing businesses.
what are common reasons for food manufacturers getting nonconformances related to document control, when they're subject to 3rd party audit?
Food manufacturers can encounter nonconformances related to document control during third-party audits for various reasons. These nonconformances indicate that the manufacturer’s document control processes do not meet the required standards or expectations. Here are some common reasons for such nonconformances:
Outdated Documents: Failing to regularly review and update documents can lead to nonconformances. Auditors expect that procedures, specifications, and other documents are current and reflect the latest industry standards.
Missing or Incomplete Documents: Incomplete or missing documents, such as standard operating procedures (SOPs), work instructions, or records, can result in nonconformances. Auditors may look for evidence of comprehensive and accurate documentation.
Inaccurate Information: Documents that contain errors, inaccuracies, or inconsistencies can raise concerns during audits. Auditors expect that information within documents will be factually correct and aligned with actual practices.
Lack of Document Control Process: If there is no formalized process for document control, including version control, approval procedures, and change management, it can lead to nonconformances. Auditors want to see a well-structured document control system in place.
Poor Access Control: Inadequate access controls can lead to unauthorised personnel making changes to critical documents. Auditors expect a system in place to prevent unauthorised access and changes.
Missing Signatures or Approvals: Documents that require authorisation or approval should have clear evidence of such actions. Failure to provide proof of appropriate signatures or approvals can lead to nonconformances.
Disorganised Document Management: Difficulty in locating and retrieving documents due to poor organisation can lead to nonconformances. Auditors expect documents to be logically organised and easily accessible.
Inconsistent Implementation: If there is a discrepancy between documented procedures and actual practices, it can result in nonconformances. Auditors want to ensure that documented processes are consistently followed.
Inadequate Training: Employees must be trained on the proper use of documented procedures. Nonconformances can occur if there is a lack of evidence of training or if employees are not following documented practices.
Failure to Address Previous Findings: If nonconformances related to document control were identified in previous audits and have not been adequately addressed, they can result in further nonconformances.
To avoid nonconformances related to document control during third-party audits, food manufacturers should establish robust document control processes, adhere to industry standards, and consistently review and update their documents to reflect accurate and current practices. Regular internal audits and self-assessments can also help identify and address potential issues before they are flagged by third-party auditors.
In Summary
In summary, document version control is essential in the food manufacturing industry to ensure that all company documents are up-to-date and accurate. This process involves establishing a system for identifying and tracking changes made to documents over time, as well as ensuring that employees have access to the most recent versions of important documents.
Effective document version control can help food manufacturers comply with regulatory and voluntary assurance scheme requirements. It also helps organisations maintain consistency in their operations by ensuring that everyone has access to current procedures, policies, and guidelines that make up the quality management system.
Overall, implementing a robust document version control system is crucial for maintaining quality standards and reducing risk in the food manufacturing industry. By keeping track of changes and ensuring that all employees have access to updated information, companies can improve efficiency while also minimising errors or discrepancies in their processes.
Further Resources
Food Industry Hub serves the food industry with a range of digital resources for the benefit of both commercial food manufacturers and food industry professionals.
For food manufacturers, we offer integrated management systems that give every user a direct interface with your QMS.
For food industry professionals, we provide an extensive signposting service in addition to informational content we hope you’ll find useful as you face new professional challenges. We have very ambitious plans to expand the range of services offered, and currently present informational content on management, safety and quality, and professional success.