Introduction
We all have targets and objectives to meet, but sometimes it can seem challenging to achieve the outcomes needed.
This is where the PDCA (Plan Do Check Act) methodology comes into play. It offers a systematic approach to achieving the management results needed for your food manufacturing business. With PDCA, you can continuously improve processes, monitor performance, and make data-driven adjustments to ensure compliance and quality control.
Table of Contents
Key Takeaways
- The PDCA methodology (Plan, Do, Check, Act) is a systematic approach to problem-solving and continuous improvement in food manufacturing businesses.
- Identifying and defining desirable management outcomes is crucial for success, including goals such as increasing production efficiency, reducing waste, improving product quality, enhancing customer satisfaction, and ensuring regulatory compliance and food safety.
- Creating an effective plan for success involves clearly defining goals, breaking them down into achievable tasks, assessing resources, setting deadlines, and involving the team.
- Implementing the PDCA methodology requires creating a detailed plan, executing necessary changes, monitoring progress, evaluating outcomes, and identifying areas for improvement.
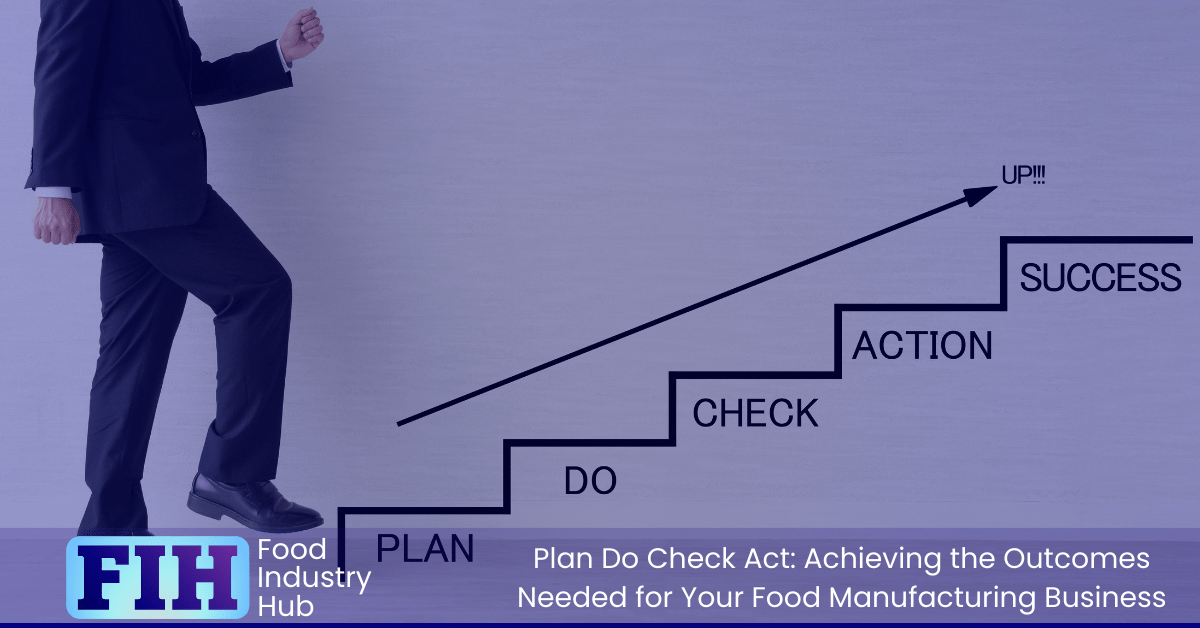
With Food Industry Hub Management Systems, you can trust your food safety processes are reliable, compliant, and audit-ready.
Understanding the PDCA Methodology
To better understand the PDCA methodology, you need to grasp its core principles and how it can be applied to improve management outcomes in food manufacturing businesses. PDCA stands for Plan, Do, Check, Act, and it’s a systematic approach to problem-solving and continuous improvement.
The first step in the PDCA methodology is planning. This involves setting clear objectives and goals. You need to identify the problem or opportunity for improvement and develop a plan to address it. This plan should include specific actions, timelines, and responsibilities.
Once the plan is in place, it’s time to move on to the second step: doing. This is where you implement the plan and carry out the actions identified. It’s important to track progress and collect data during this phase to evaluate the effectiveness of the actions taken.
After implementing the plan, the next step is to check. This involves analysing the data collected to determine whether the actions taken have resulted in the desired outcomes. If the results aren’t as expected, adjustments can be made to the plan.
The final step in the PDCA methodology is acting. Based on the results of the check phase, you can make informed decisions on whether to continue with the plan, modify it, or abandon it altogether. This step ensures that the improvements made are sustainable and continue to deliver positive management outcomes.
Identifying Desirable Management Outcomes for Your Food Manufacturing Business
Now that you have a solid understanding of the PDCA methodology and its application in improving management outcomes, let’s focus on identifying the desirable outcomes for your food manufacturing business.
The first step in this process is to define what success looks like for your business. Start by considering the overall goals and objectives you want to achieve. Do you want to increase production efficiency, reduce waste, improve product quality, or enhance customer satisfaction? Identifying these desired outcomes will help guide your decision-making process and ensure that your efforts are aligned with your business goals.
Next, think about the specific metrics or key performance indicators (KPIs) that are relevant to the food sector. These could include things like on-time delivery, production yield, customer complaints, or employee productivity. By tracking and monitoring these metrics, you can gauge your progress towards achieving your desired outcomes and make data-driven decisions to optimise your operations.
Consider the importance of regulatory compliance and food safety in the food industry. Ensuring that your products meet all necessary standards and regulations is vital for the success and reputation of your business. Make sure to include these outcomes in your list of desirable management outcomes.
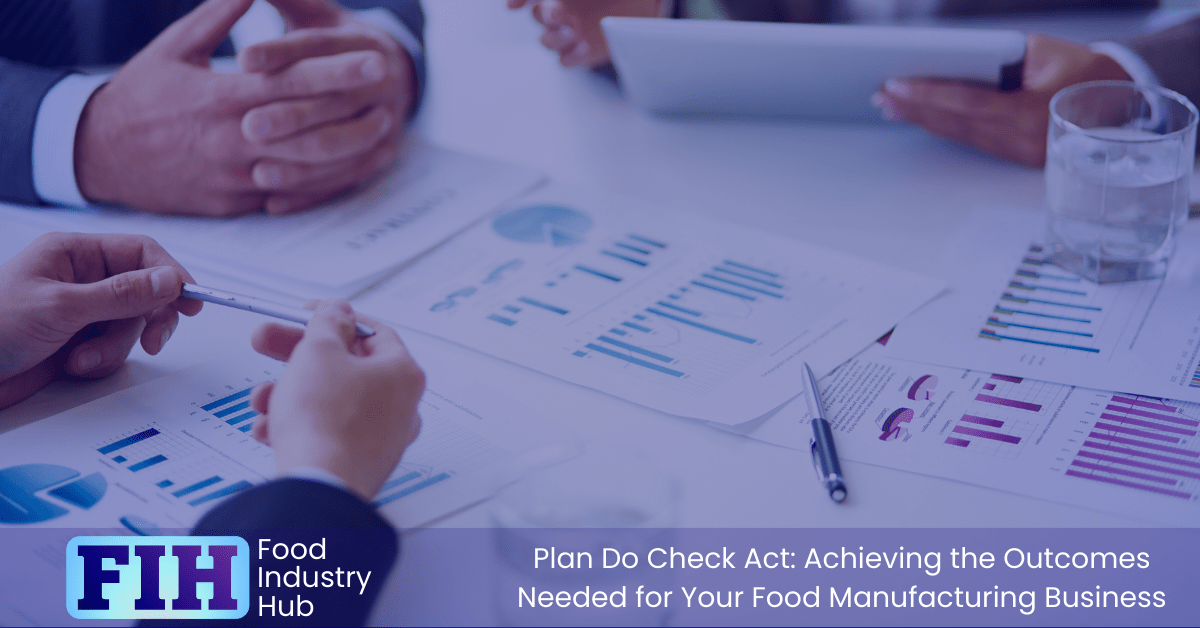
Forming a Strategy – The ‘Plan’ Stage
Drawing up an actionable plan to ensure your food manufacturing business achieves its desired outcomes begins with careful planning.
Start by clearly defining your goals and objectives. What do you want to achieve? Do you want to increase production, improve product quality, or expand your market share?
Once you have identified your goals, break them down into smaller, achievable tasks. This will make the planning process more manageable and help you stay focused.
Next, consider the resources you have at your disposal. Assess your current staff, equipment, and facilities. Do you have the necessary resources to achieve your goals? If not, what do you need to acquire or invest in? Be realistic about what’s achievable given your available budget.
In addition to setting goals and assessing resources, it’s crucial to create a timeline for your plan. Set deadlines for each task and track your progress regularly. All actions should consist of SMART goals. This will help you stay on track and ensure that you’re making steady progress towards your desired outcomes.
Involve your team in the planning process. By including their input and feedback, you can create a more comprehensive plan that takes into account different perspectives and expertise. This will also help build a sense of ownership and commitment to the plan.

Sign-up for the Food Industry Hub Mail Service
We regularly produce new content for food industry professionals, and the Food Industry Hub Mail Service is the best way to stay up to date with the latest additions.
Signup today to be added to the Food Industry Hub mailing list.
Implementation – The ‘Do’ Stage
Implementing the PDCA methodology can help you to effectively manage and improve your operations, resulting in increased efficiency, quality, and profitability.
The ‘Do’ phase involves executing the plan and implementing the necessary changes. This may include training employees, updating procedures, or investing in new equipment. It’s crucial to monitor the progress during this phase to ensure that everything is going as planned.
The implementation stage is simply the application of the plan that was established in the previous stage – so the success of the ‘do’ stage of PDCA rests on the quality and appropriateness of the plan formed. You can evaluate how well the implementation stage is carried out by how closely the actions performed match the plan, including measurables like adherence to schedule.
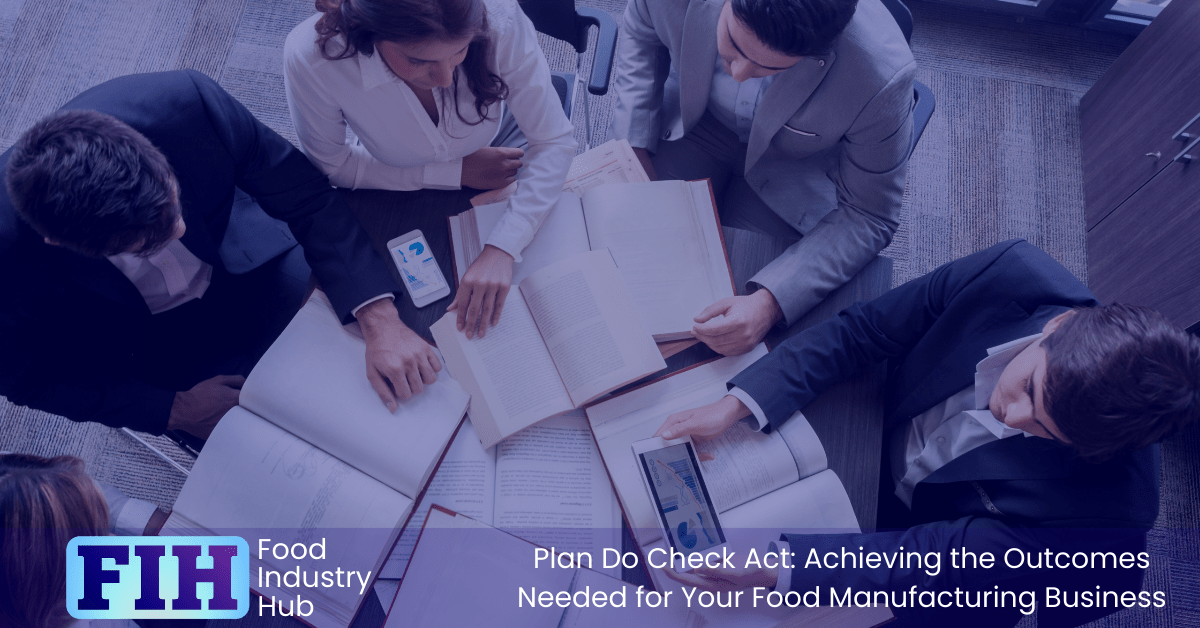
Monitoring and Measuring Performance – The ‘Check’ Stage
To effectively monitor and measure the performance of your PDCA approach, establish clear metrics and regularly track key indicators. You can gain valuable insights into the efficiency and effectiveness of your operations, identify areas for improvement, and make an informed assessment of the suitability of the plan and actions taken.
It’s important to identify the right metrics that align with your plan and actions. These metrics should be chosen to accurately reflect the success or failure of planned actions – so whether or not the actions taken elicit the desired results. By clearly defining these metrics, you can set benchmarks and targets that will enable you to track progress and evaluate the success of your PDCA cycle.
In addition to tracking performance metrics, it’s also important to analyse the data collected and draw meaningful insights from it. This analysis can help you identify trends, patterns, and areas of improvement within your business processes. By leveraging this information, you can make data-driven decisions that will lead to improved efficiency, productivity, and ultimately, commercial success.
Thoroughly examine the data collected and draw actionable insights from it. Look to identify trends, patterns, and areas of improvement that will help you make informed decisions for your business.
Organise the data in a logical manner – for example, by creating spreadsheets or charts that allow for easy comparison and analysis. The idea is to use the insights gained from the analysis to develop and implement strategies, initiatives, or changes that will positively impact your business performance.
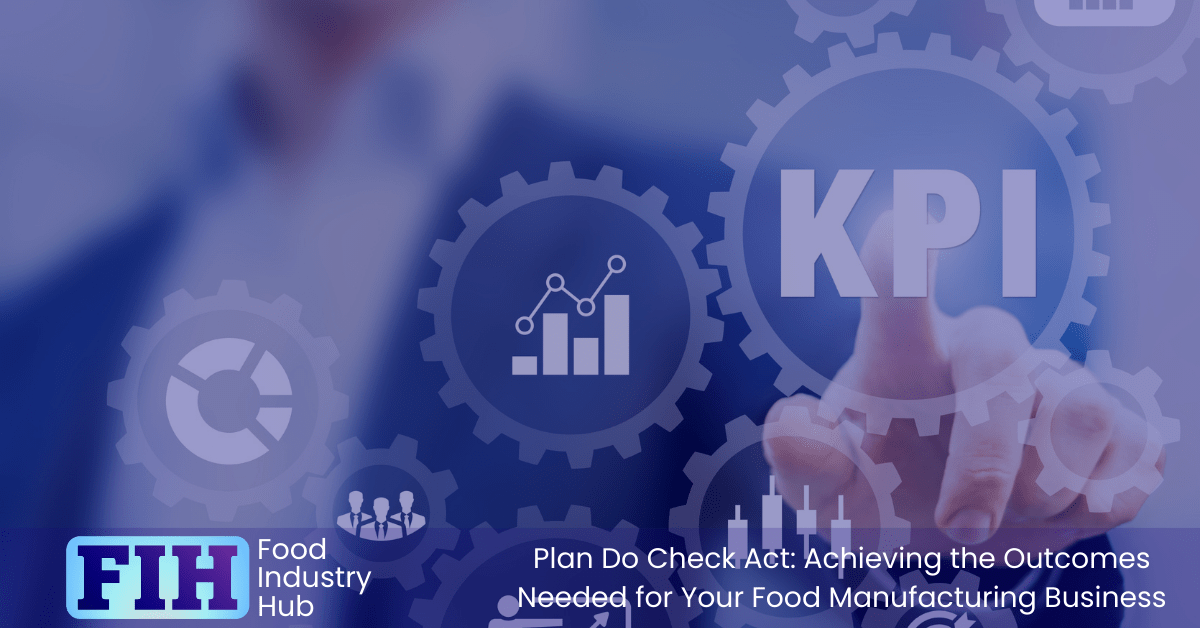
Making Data-Driven Adjustments – The ‘Act’ Stage
Utilising the data collected and analysing it thoroughly positions you to assess the appropriateness of the plan and the effectiveness of the actions taken.
At the beginning of the PDCA cycle, you form a plan that you predict will lead to desired outcomes when implemented – so if it turns out that the prediction was incorrect, the ‘act’ stage is an opportunity to make adjustments based on new information.
It is important to note that making data-driven adjustments is an ongoing process. Regularly collecting and analysing data will allow you to monitor the effectiveness of your adjustments and make further refinements as needed. By embracing a data-driven approach, you can continuously improve your ongoing improvement plans.
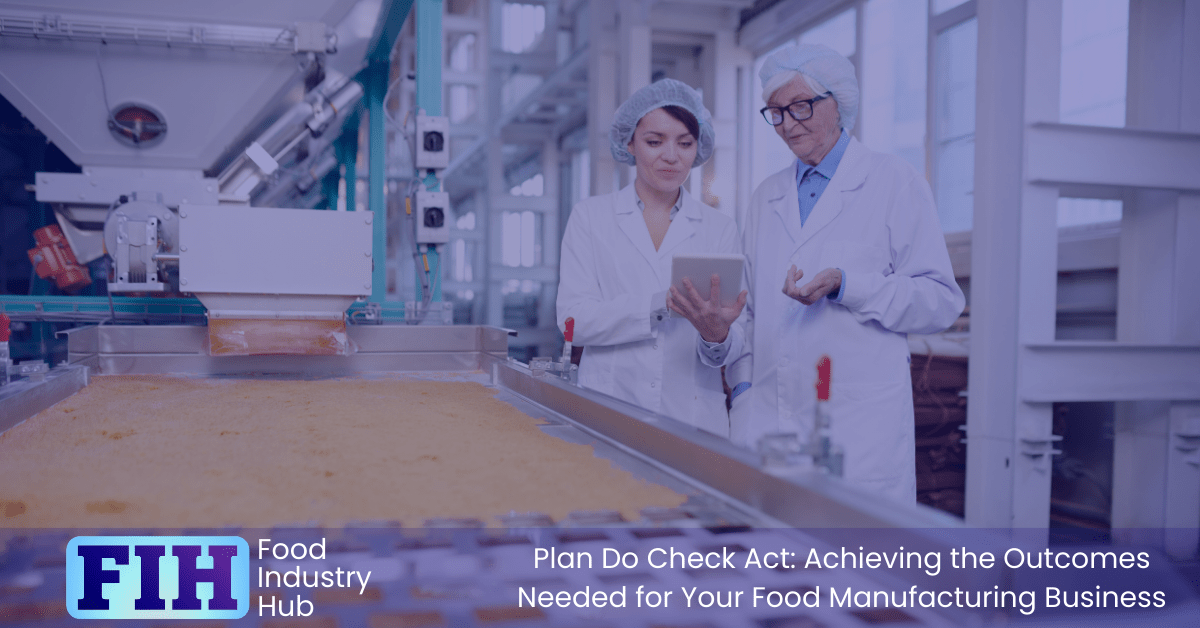
Continuous Improvement for Sustainable Success
Achieving sustainable success in your food manufacturing business requires a commitment to continuous improvement. Simply maintaining the status quo isn’t enough. To stay ahead and meet the evolving demands of customers and consumers, you must constantly strive to improve your processes, products, and overall performance.
Continuous improvement involves regularly evaluating your operations, identifying areas for enhancement, and implementing changes to drive positive outcomes. This approach enables you to adapt to market trends, enhance efficiency, reduce waste, and ultimately increase profitability.
Using a structured approach to continuous improvement, such as the Plan Do Check Act (PDCA) cycle, can help bring a sense of direction for continuous improvement efforts. This cycle involves planning your improvement initiatives, executing them, evaluating the results, and then taking appropriate actions based on the feedback received. By following this iterative process, you can make incremental improvements over time, leading to sustainable success.
In Summary
You have learned the power of the PDCA methodology for achieving management outcomes in your food manufacturing business.
By understanding, creating, implementing, monitoring, and adjusting, you can ensure compliance, quality control, and continuous improvement.
Embrace this approach to drive sustainable success and evoke a sense of empowerment, satisfaction, and growth throughout your team.
Further Resources
Food Industry Hub serves the food industry with a range of digital resources for the benefit of both commercial food manufacturers and food industry professionals.
For food manufacturers, we offer integrated management systems that give every user a direct interface with your QMS.
For food industry professionals, we provide an extensive signposting service in addition to informational content we hope you’ll find useful as you face new professional challenges. We have very ambitious plans to expand the range of services offered, and currently present informational content on management, safety and quality, and professional success.