Introduction
Implementing TQM in your food manufacturing processes can lead to a culture of continuous improvement, where every employee is committed to delivering products that meet or exceed customer expectations. By focusing on customer satisfaction, TQM helps food manufacturers identify areas for improvement, streamline processes, and reduce waste, ultimately leading to higher quality products.
TQM emphasises the importance of data-driven decision-making. By collecting and analysing data at every stage of production, manufacturers can identify trends, anticipate potential issues, and make proactive decisions to ensure consistent quality. This data-driven approach also enables companies to set measurable quality objectives, track performance against these objectives, and make adjustments as needed to stay on course.
Total quality management promotes a collaborative work environment where employees are encouraged to communicate openly, share ideas, and work together towards common quality goals. This teamwork not only improves morale and employee satisfaction but also fosters innovation and creativity, leading to new ways to enhance product quality and efficiency.
Table of Contents
Key Takeaways
- TQM enhances quality, efficiency, and consistency in food production.
- Focus on customer requirements to build trust and loyalty.
- Promotes teamwork, collaboration, and continuous improvement culture.
- Data-driven decision-making ensures consistent quality standards.
- Improves morale, employee satisfaction, and product quality in food manufacturing.
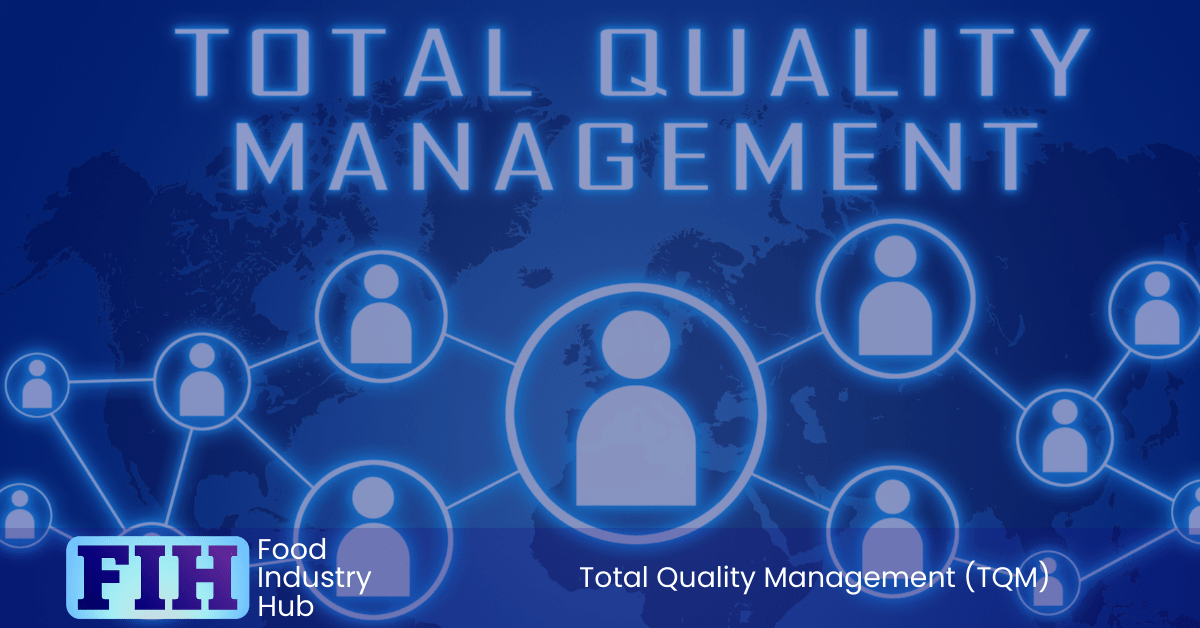
Enhance your food manufacturing operations with Food Industry Hub Management Systems, built to improve quality assurance and streamline compliance.
Principals of Total Quality Management (TQM)
Total Quality Management (TQM) focuses on the roles customer satisfaction, employee engagement, and process management play in achieving organisational excellence.
By implementing the principles of Total Quality Management (TQM) in your organisation, you can strive for customer satisfaction, engage employees, optimise processes, align quality with strategic goals, utilise improvement tools, make data-driven decisions, and promote transparency.
These practices won’t only improve the quality of your products and services but also foster a culture of innovation and continuous improvement, leading to long-term success in the food industry.
- Customer satisfaction focus as primary goal.
- Employee engagement in quality improvement.
- Process management for continuous improvement.
- Integration of quality management in all functions.
- Alignment with strategic goals for success.
Striving For Customer Satisfaction as The Primary Goal
Focusing on achieving customer satisfaction is a fundamental aspect of implementing Total Quality Management (TQM). Customer satisfaction is the cornerstone of TQM because it drives business success. By understanding and meeting customer needs and expectations, companies can build long-lasting relationships, increase loyalty, and gain a competitive edge in the market.
To achieve customer satisfaction, organisations must prioritise quality in all aspects of their products and services.
Organisations must focus on continuous improvement to maintain high levels of customer satisfaction. TQM emphasises the importance of ongoing evaluation, monitoring, and refinement of processes to enhance quality and meet changing customer needs. By constantly seeking ways to improve products and services, companies can stay ahead of competitors and retain customer loyalty.
Engaging All Employees at All Levels in The Quality Improvement Process
Every member of the organisation plays a vital role in contributing to the overall quality standards. By involving all employees in the quality improvement process, you not only harness a diverse range of perspectives and ideas but also foster a culture of collective responsibility towards quality.
Engaging employees at all levels begins with effective communication. Clearly convey the goals, processes, and benefits of TQM to ensure everyone understands their role in the quality improvement journey. Encourage open dialogue, feedback, and suggestions from employees to continuously refine and enhance quality practices.
Empower employees by providing them with the necessary training, resources, and authority to make quality-related decisions. Recognise and reward individuals and teams for their contributions to quality improvement initiatives, building a sense of ownership and motivation to excel.
Process Management: Processes That Can Be Defined, Measured, Analysed, Improved, and Controlled
Effective Total Quality Management (TQM) hinges on the ability to define, measure, analyse, improve, and control processes. Process management is a crucial aspect of TQM, as it enables companies to streamline operations, enhance efficiency, and deliver consistent quality to customers.
Defining processes involves clearly outlining the steps, inputs, outputs, and responsibilities involved in a particular task or workflow. This clarity ensures that everyone understands their role and how it contributes to the overall objectives of the business.
Once processes are defined, the next step is measurement. This involves collecting data on key performance indicators (KPIs) to assess how well a process is functioning.
After measurement comes analysis, where the collected data is evaluated to identify areas of improvement. This analysis helps pinpoint bottlenecks, inefficiencies, or deviations from standards. Once opportunities for improvement are identified, organisations can implement changes to enhance the process.
Control is the final step in process management, where systems are put in place to ensure that the improvements are sustained over time. By monitoring performance and implementing corrective actions when necessary, companies can maintain the quality gains achieved through process improvement initiatives.
Sign-up for the Food Industry Hub Mail Service
We regularly produce new content for food industry professionals, and the Food Industry Hub Mail Service is the best way to stay up to date with the latest additions.
Signup today to be added to the Food Industry Hub mailing list.
Integrating Quality Management into All Functions and Departments
Quality management integration across all functions and departments is fundamental to achieving organisational excellence and customer satisfaction in Total Quality Management (TQM). By incorporating quality management principles into every aspect of your organisation, you ensure that all processes and activities are geared towards delivering high-quality products that meet or exceed customer expectations.
Integrating quality management into all functions and departments requires a systematic approach. It involves establishing clear quality objectives, defining quality standards, and implementing quality control measures throughout the organisation. This integration ensures that quality becomes a core value of your company and is embedded in every operation and decision-making process.
When quality management is integrated into all functions and departments, it helps to establish a culture of continuous improvement. Employees at all levels become actively engaged in identifying areas for enhancement, implementing quality initiatives, and monitoring outcomes. This collaborative approach not only leads to higher product or service quality but also boosts employee morale and productivity.
Integrating quality management into all functions and departments helps in streamlining processes and eliminating inefficiencies. By identifying and addressing quality issues at an early stage, organisations can prevent defects, reduce waste, and optimise resources. This proactive approach not only enhances overall operational efficiency but also contributes to cost savings and increased profitability.
Aligning Quality Management with The Organisation’s Strategic Goals and Objectives
Aligning quality management with your organisation’s strategic goals and objectives is essential for driving sustainable growth and competitive advantage in the food manufacturing industry. By ensuring that quality management practices are directly linked to the overarching mission and vision of your organisation, you can create a strong foundation for success.
To align quality management with strategic goals, start by clearly defining your organisation’s objectives and understanding how quality impacts each of them. Identify key performance indicators (KPIs) that measure quality in relation to these goals. For example, if one of your strategic objectives is to increase customer satisfaction, you may track metrics such as customer complaints, product returns, or Net Promoter Score (NPS).
From top management setting the strategic direction to frontline employees implementing quality initiatives, everyone must understand how their roles contribute to achieving the organisation’s strategic goals through quality management.
Regularly review and adjust your quality management processes to ensure they remain aligned with evolving strategic objectives. This ongoing alignment will help drive continuous improvement, enhance overall performance, and ultimately lead to sustainable success.
Using Tools Like Plan-Do-Check-Act (PDCA) Cycle for Continuous Improvement
Utilising tools like the Plan-Do-Check-Act (PDCA) cycle is an obvious choice for driving continuous improvement within your organisation’s quality management processes. The PDCA cycle consists of four key steps: Plan, Do, Check, and Act.
In the planning phase, you identify areas for improvement and establish objectives. This sets the foundation for the next step, where you implement the planned changes.
The Check phase involves monitoring and evaluating the results to ensure they align with the set objectives. Based on this evaluation, in the Act phase, you make necessary adjustments to further enhance the processes.
By following the PDCA cycle, you create a structured approach to improving quality management. This methodical cycle promotes a culture of continuous improvement by encouraging ongoing assessment and refinement.
Regularly applying the PDCA cycle allows your organisation to adapt to changing circumstances, respond to feedback, and optimise operations effectively.
Integrating the PDCA cycle into your quality management approach fosters a proactive mindset within your team. It empowers employees to actively participate in identifying areas for enhancement and implementing solutions.
Ultimately, the PDCA cycle promotes efficiency, innovation, and overall quality excellence within your organisation’s operations.
Using Accurate Data and Analysis to Guide Decision-Making Processes
Utilising accurate data allows you to understand the current state of affairs within your organisation. This data can include various metrics such as sales figures, customer feedback, production efficiency, and financial performance. By analysing this data, you can identify trends, patterns, and areas for improvement.
Accurate data and analysis also enable you to make data-driven decisions rather than relying on assumptions or gut feelings. This approach helps in reducing the risk of making decisions based on incomplete or misleading information. Moreover, it allows you to prioritise initiatives based on their potential impact on the organisation’s overall performance.
When it comes to decision-making processes, accurate data and analysis provide a solid foundation for evaluating different options. By comparing potential outcomes and assessing risks, you can choose the most suitable course of action. Additionally, accurate data enables you to track the results of your decisions, allowing you to adjust strategies as needed to achieve desired outcomes.
In essence, using accurate data and analysis ensures that your decisions are well-informed, strategic, and aligned with your organisation’s goals.
Promoting Transparency and Openness to Facilitate Quality Improvements
Transparency involves sharing information openly, while openness pertains to creating a culture where feedback and ideas can flow freely. By promoting transparency, you allow employees to understand the organisation’s goals, strategies, and performance metrics. This clarity enables them to align their efforts with the overall objectives, leading to more efficient processes and better outcomes.
Openness encourages employees to voice their opinions, concerns, and suggestions without fear of reprisal. This free exchange of ideas fosters innovation, problem-solving, and continuous learning. When employees feel heard and valued, they’re more likely to engage actively in quality improvement initiatives. Openness can uncover issues that may otherwise remain hidden, allowing for timely interventions and preventing potential quality lapses.
To facilitate transparency and openness, you can implement practices such as regular meetings, anonymous suggestion boxes, open-door policies, and transparent performance evaluations.
Additionally, leveraging technology for communication and feedback mechanisms can enhance transparency and openness in today’s digital age.
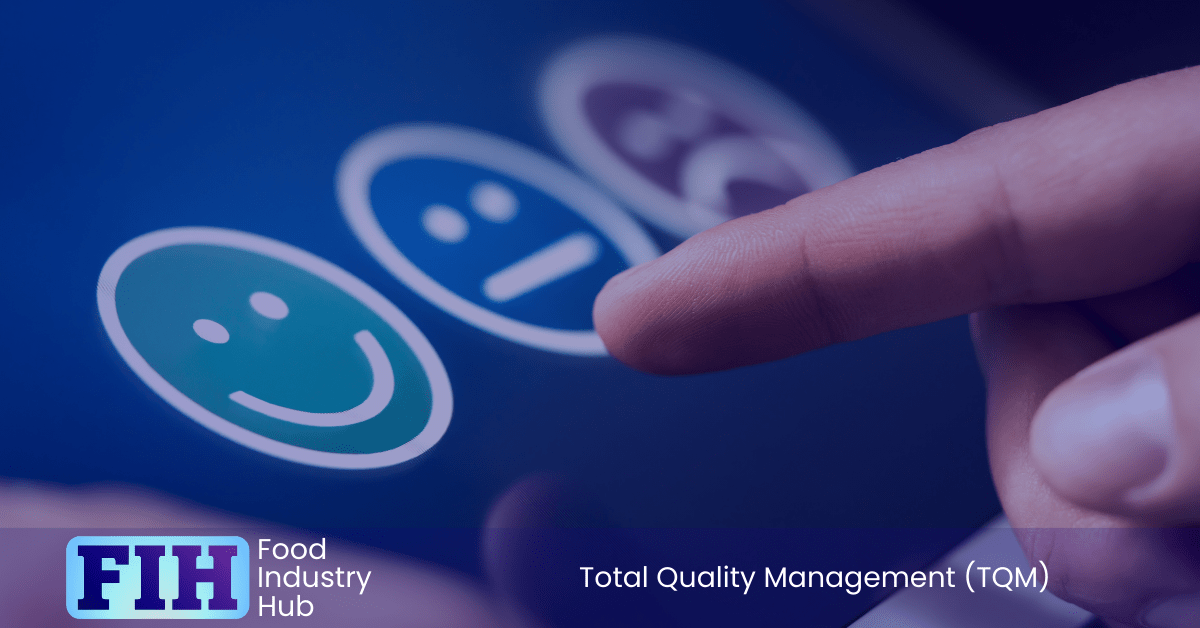
Total Quality Management (TQM) Tools and Techniques
You might be intrigued by the multitude of Total Quality Management (TQM) tools and techniques available to enhance your organisation’s performance. From Quality Circles to Pareto Analysis, each method offers a unique approach to driving excellence and efficiency. By implementing these tools strategically, you can not only pinpoint areas for improvement but also elevate your processes to meet and exceed customer expectations. The journey towards mastering TQM tools and techniques is a path paved with continuous learning and refinement, ultimately leading to a culture of relentless quality improvement.
By implementing Total Quality Management tools and techniques such as Quality Circles, Benchmarking, SPC, FMEA, Pareto Analysis, and Root Cause Analysis, organisations can enhance their processes, products, and services to achieve continuous improvement and customer satisfaction.
These tools provide practical methods for identifying areas of improvement, analysing data, and prioritising actions to drive organisational excellence.
- Quality Circles enhance collaboration and problem-solving.
- Benchmarking adopts best practices for improvement.
- Statistical Process Control (SPC) reduces process variation.
- Failure Mode and Effects Analysis (FMEA) prevents failures proactively.
- Pareto Analysis prioritises critical factors for improvement.
Quality Circles
Quality Circles, also known as QC groups, are small groups of employees who come together to identify, analyse, and solve work-related issues within an organisation. Quality circles provide a platform for employees to collaborate, share ideas, and contribute to continuous improvement efforts. Quality Circles can be a powerful tool for driving positive change within an organisation.
One key benefit of Quality Circles is the diverse perspectives that members bring to the table. With employees from different departments or levels of the organisation participating, these groups can offer a holistic view of the issues at hand. This diversity can lead to more creative solutions and a deeper understanding of the root causes of problems.
Furthermore, Quality Circles promote a culture of collaboration and teamwork. By working together towards a common goal, employees develop stronger bonds and communication skills. This not only enhances problem-solving abilities within the group but also improves overall organisational cohesion.
Benchmarking
To improve your organisation’s performance and competitiveness, consider utilising benchmarking as a strategic tool for evaluating and adopting best practices from industry leaders. Benchmarking involves comparing your processes, products, or services against those of top-performing companies in your industry or even in other industries to identify areas for improvement.
By analysing the practices of successful organisations, you can gain valuable insights into what works well and how you can implement similar strategies within your own company.
There are different types of benchmarking that you can employ, such as internal benchmarking (comparing processes within your organisation), competitive benchmarking (evaluating against direct competitors), functional benchmarking (looking at specific functions within different companies), and generic benchmarking (comparing with organisations outside your industry). Each type has its own benefits and can provide unique perspectives on where your organisation stands in comparison to others.
Benchmarking isn’t about blindly copying what others do but rather about understanding why certain practices lead to success and how you can adapt them to fit your own context. It can help you set realistic performance goals, prioritise areas for improvement, and drive innovation.
Statistical Process Control (SPC)
Statistical Process Control (SPC) allows organisations to monitor and improve their processes systematically through data analysis and variation reduction. By utilising SPC techniques, you can effectively track process performance in real-time, enabling you to detect any deviations or abnormalities promptly. This proactive approach empowers you to make informed decisions and take corrective actions before issues escalate, ultimately enhancing overall process efficiency and product quality.
One key aspect of SPC is the use of control charts, such as X-bar and R charts, which provide a visual representation of process data over time. These charts help you identify trends, outliers, and patterns that signify whether a process is in control or requires adjustment. Through the analysis of these control charts, you can pinpoint areas for improvement, set performance benchmarks, and ensure consistency in output quality.
SPC aids in reducing process variation by distinguishing between common cause variation (inherent to the process) and special cause variation (resulting from external factors). This differentiation enables you to focus on addressing specific sources of variation that impact product quality, leading to more stable and predictable processes.
In essence, integrating Statistical Process Control into your quality management practices fosters a data-driven culture that promotes continuous improvement and sustains high levels of operational performance.
Failure Mode and Effects Analysis (FMEA)
Failure Mode and Effects Analysis (FMEA) can systematically identify potential failure modes within your processes and evaluate their effects to prioritise improvement efforts effectively. FMEA is a proactive approach that helps organisations anticipate and prevent failures before they occur.
The process involves breaking down a system, product, or service into its components, analysing how each component could fail, determining the potential effects of those failures, and then prioritising actions based on the severity of the consequences.
FMEA consists of three main types:
System FMEA focuses on the entire system, identifying how failures at the system level could impact overall performance.
Design FMEA examines how potential design weaknesses could lead to failures in the product or service.
Process FMEA looks at failure modes within the manufacturing or service delivery processes.
Pareto Analysis
Named after Vilfredo Pareto, an Italian economist, Pareto Analysis is a powerful tool used in quality management to identify and focus on the most critical issues affecting a process.
The underlying principle of Pareto Analysis is the Pareto Principle, also known as the 80/20 rule, which suggests that roughly 80% of effects come from 20% of the causes.
By applying Pareto Analysis, you can visually represent and quantify the impact of various factors on a specific outcome. This analysis helps you allocate your resources effectively by directing your attention to the factors that will yield the most significant improvements. By identifying the vital few factors, you can concentrate your efforts on addressing the root causes that will have the most substantial positive impact on your process performance.
To conduct a Pareto Analysis, gather relevant data on the different factors influencing your process, categorise them, and then plot them on a Pareto chart. This chart will help you visually identify the most critical factors that require immediate attention.
Prioritising impact allows you to focus your improvement efforts efficiently, leading to enhanced overall process performance.
Root Cause Analysis
How can you systematically identify the fundamental reasons behind process issues to drive meaningful improvements? Root Cause Analysis (RCA) is a powerful tool that allows you to delve deep into the underlying causes of problems rather than just addressing the symptoms. By using RCA, you can uncover the root causes that, when addressed, can prevent issues from reoccurring and lead to sustainable improvements.
To conduct an effective RCA, start by defining the problem clearly and comprehensively. Gather relevant data and involve team members who’ve got a good understanding of the process. Then, use techniques such as the ‘5 Whys’ to iteratively explore cause-and-effect relationships until you reach the fundamental reason behind the issue. By asking ‘why’ multiple times, you can peel back the layers of causation to reveal the core issue.
It’s essential to prioritise the identified root causes based on their impact and feasibility of addressing them. Focus on addressing the most critical root causes first to achieve significant results. Implement corrective actions that target these root causes and monitor their effectiveness over time.
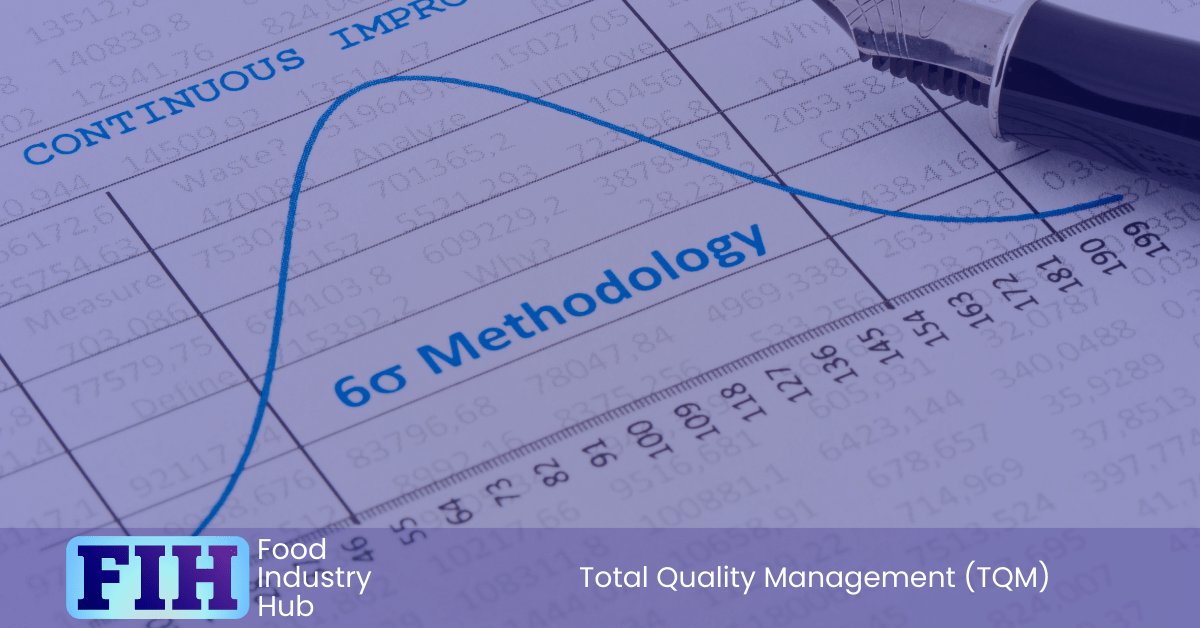
Benefits of Total Quality Management (TQM)
The benefits are not just theoretical; they have tangible impacts on your product quality, customer satisfaction, and bottom line. Implementing TQM isn’t just a trend; it’s a strategic move that can set you apart from competitors and drive sustainable growth.
Implementing Total Quality Management (TQM) in your organisation can bring about a multitude of benefits. These include improved product and service quality, increased customer satisfaction, higher employee morale, better operational efficiency, competitive advantage, and ultimately, long-term success and growth in the food industry.
By focusing on continuous improvement and employee involvement, TQM can help you achieve your business goals and stay ahead of the competition in today’s demanding marketplace.
- Enhanced product and service quality through continuous improvement and employee involvement.
- Increased customer satisfaction and loyalty by meeting high-quality standards and tailoring offerings.
- Improved employee morale and engagement with open communication and training support.
- Better operational efficiency achieved by streamlining processes and reducing waste.
- Competitive advantage and market share growth driven by high-quality offerings and innovation.
Improved Product and Service Quality
Implementing Total Quality Management (TQM) processes in your organisation can result in a significant enhancement in the quality of your products and services. By focusing on continuous improvement and the involvement of every employee in quality initiatives, TQM ensures that your organisation’s products meet or exceed customer expectations.
Through the implementation of TQM practices such as process mapping, root cause analysis, and statistical process control, you can identify areas for improvement and take proactive steps to address them.
TQM emphasises the importance of customer feedback and satisfaction in driving quality improvements. By closely monitoring customer preferences and addressing their concerns promptly, you can tailor your products and services to better meet their needs.
This customer-centric approach not only enhances the quality of your offerings but also fosters greater customer loyalty and retention.
Increased Customer Satisfaction and Loyalty
Enhancing customer satisfaction and fostering loyalty are key outcomes of implementing Total Quality Management (TQM) practices in your organisation. By focusing on meeting and exceeding customer expectations, TQM helps in improving the overall customer experience.
When products and services consistently meet high-quality standards, customers are more likely to be satisfied with their purchases, leading to increased loyalty and repeat business.
TQM emphasises the importance of understanding customer needs and preferences, which allows organisations to tailor their offerings accordingly. This customer-centric approach not only helps in delivering superior value to customers but also in building long-term relationships based on trust and satisfaction.
As a result, satisfied customers will be more inclined to recommend your products or services to others, further expanding your customer base.
By consistently delivering high-quality products and services, organisations can differentiate themselves from competitors, creating a competitive advantage that’s difficult to replicate. This competitive edge, coupled with enhanced customer satisfaction and loyalty, can lead to increased profitability and sustainable growth.
Enhanced Employee Morale and Engagement
High levels of employee morale and engagement are intrinsic outcomes of integrating Total Quality Management (TQM) principles. When employees feel valued and empowered to contribute meaningfully to the organisation’s success through TQM practices, their morale receives a significant boost.
TQM fosters a culture of open communication, continuous improvement, and teamwork, which in turn enhances employee engagement by providing a sense of purpose and involvement in decision-making processes.
TQM emphasises the importance of training and development, ensuring that employees have the necessary skills to excel in their roles. This commitment to employee growth not only increases morale but also enhances engagement as individuals feel supported and motivated to perform at their best.
Better Operational Efficiency and Reduced Waste
Total Quality Management (TQM) emphasises the importance of streamlining processes, reducing and controlling defects, and continuously improving operations. Through methods like Six Sigma and Lean practices, organisations can identify inefficiencies, bottlenecks, and sources of waste in their workflows.
Reducing waste directly impacts your bottom line by cutting unnecessary costs and optimising resource utilisation. By fostering a culture of quality and efficiency, TQM can help you deliver products and services to customers faster and with higher quality. This not only enhances customer satisfaction but also boosts your reputation in the market.
Operational efficiency improvements gained through TQM can result in shorter lead times, reduced cycle times, and increased productivity. By focusing on quality and waste reduction, you can enhance your competitiveness, drive innovation, and adapt more effectively to changing market demands. Embracing TQM principles can set you on a path towards operational excellence and sustainable growth.
Competitive Advantage and Market Share Growth
By focusing on customer satisfaction, continuous improvement, and employee involvement, TQM allows companies to differentiate themselves from competitors and capture a larger portion of the market.
TQM helps companies stand out by consistently delivering high-quality products or services that meet or exceed customer expectations. This leads to enhanced customer loyalty, positive word-of-mouth promotion, and an improved brand reputation. As a result, organisations practicing TQM often experience increased market share as more customers choose their offerings over alternatives.
TQM fosters innovation and agility within the organisation, enabling quicker responses to market changes and customer needs. This flexibility can give companies a competitive edge by adapting faster than competitors and seizing opportunities before others can.
Ultimately, by prioritising TQM principles, businesses can strengthen their position in the market, attract more customers, and drive sustainable growth over time.
Higher Profitability and Long-Term Success
By focusing on quality at every level of your operations, you can reduce costs associated with rework, defects, and inefficiencies. This cost-saving aspect directly impacts your bottom line, leading to higher profitability.
TQM emphasises meeting customer expectations and delivering superior products or services. This customer-centric approach not only fosters loyalty but also attracts new customers through positive word-of-mouth and reputation building. As a result, your organisation can experience increased sales and market share, contributing further to your profitability.
In the long term, the commitment to quality instilled by TQM creates a culture of continuous improvement within your organisation. This ongoing quest for excellence ensures that you stay ahead of competitors, adapt to changing market dynamics, and remain relevant and successful in the food industry.
Ultimately, the higher profitability achieved through TQM practices sets the foundation for sustained success and growth.
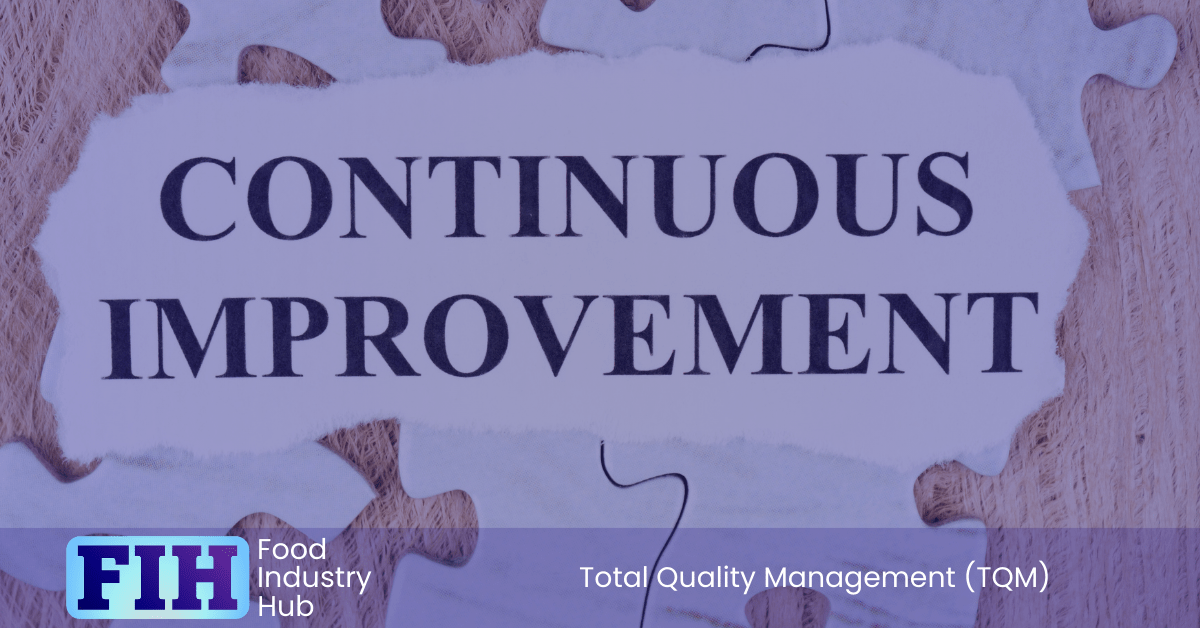
Challenges in Implementing Total Quality Management (TQM)
When implementing Total Quality Management (TQM), you’ll encounter challenges that demand proactive solutions for success. Resistance to change and initial costs can be significant roadblocks that require careful navigation. However, the real test lies in fostering a quality-oriented culture within your organisation, requiring steadfast commitment and effective leadership. The journey towards TQM implementation is complex, but understanding and overcoming these challenges is crucial for achieving lasting results.
Addressing resistance to change, managing initial costs, fostering a quality-oriented culture, and ensuring ongoing leadership support are essential for successfully implementing Total Quality Management (TQM) in a food manufacturing business.
By recognising and overcoming these challenges, you can pave the way for a culture of continuous improvement and innovation, ultimately driving long-term success and growth.
Stay proactive, stay committed, and stay focused on the goal of achieving excellence through TQM.
- Resistance to change due to fear and scepticism.
- Initial costs for training and system development.
- Cultural shift towards quality-oriented thinking required.
- Continuous leadership commitment and support needed.
- Open communication and employee involvement crucial.
Resistance to Change from Employees and Management
Employees and management often exhibit resistance to change when implementing Total Quality Management (TQM), hindering the smooth transition to a new quality-focused approach. Resistance can stem from various factors, including fear of the unknown, concerns about increased workload, or scepticism about the benefits of TQM.
To address this resistance effectively, it’s crucial to communicate openly and transparently about the reasons behind the change and the potential positive outcomes for both individuals and the organisation as a whole. Providing training and support to help employees and management understand the principles of TQM and how it aligns with organisational goals can also mitigate resistance.
Involving employees and management in the decision-making process and seeking their input on how TQM can be implemented successfully can increase buy-in and commitment to the new approach. By fostering a culture of collaboration, trust, and continuous improvement, organisations can overcome resistance to change and pave the way for a successful TQM implementation.
Initial Costs and Resource Allocation for Training and Systems Development
Allocating resources for training and systems development when implementing Total Quality Management (TQM) requires careful planning and strategic decision-making. Initially, there will be costs associated with training employees on TQM principles, methodologies, and tools. These costs may include hiring external consultants, providing internal training sessions, and potentially investing in specialised software for quality management. It’s crucial to allocate sufficient funds to ensure that employees are equipped with the necessary knowledge and skills to effectively implement TQM practices within the organisation.
Resource allocation for systems development is another critical aspect. This involves investing in technology and infrastructure to support TQM initiatives such as data collection, analysis, and reporting systems. Additionally, there may be costs associated with customising existing systems or implementing new ones tailored to TQM requirements.
Necessity for a Cultural Shift Towards Quality-Oriented Thinking
To successfully implement Total Quality Management (TQM), you must foster a cultural shift towards prioritising quality-oriented thinking throughout all levels of the company. This shift involves instilling a mindset where quality is seen as a fundamental aspect of every process, product, and service. It requires employees to understand that quality isn’t just the responsibility of a specific department but a collective effort that contributes to the overall success of the organisation.
Creating a quality-oriented culture involves clear communication of quality objectives, regular training on quality principles, and recognition of employees who exemplify quality standards. Leaders play a crucial role in driving this cultural shift by setting the example and integrating quality into the company’s values and vision.
Continuous Commitment and Leadership Support Required for Sustainability
Sustaining Total Quality Management (TQM) requires a continuous commitment from leadership to provide unwavering support and guidance throughout the organisation. For TQM to be successful in the long term, leaders must consistently demonstrate their dedication to quality improvement initiatives. This involves not only endorsing TQM principles but also actively participating in the implementation process.
Leadership support is crucial for fostering a culture that values quality and continuous improvement. By consistently championing TQM practices, leaders set the tone for the entire organisation and encourage employees to embrace quality-oriented thinking in their daily work.
Effective leaders also play a key role in ensuring that TQM strategies are integrated into all levels of the organisation, from the top management to frontline employees.
Leadership commitment is essential for overcoming resistance to change and maintaining momentum during challenging times. By staying engaged and providing ongoing support, leaders can help sustain the momentum of TQM efforts and drive continuous improvement across the organisation.
Ultimately, leadership support is the linchpin for the sustainability of TQM practices and the achievement of long-term success.
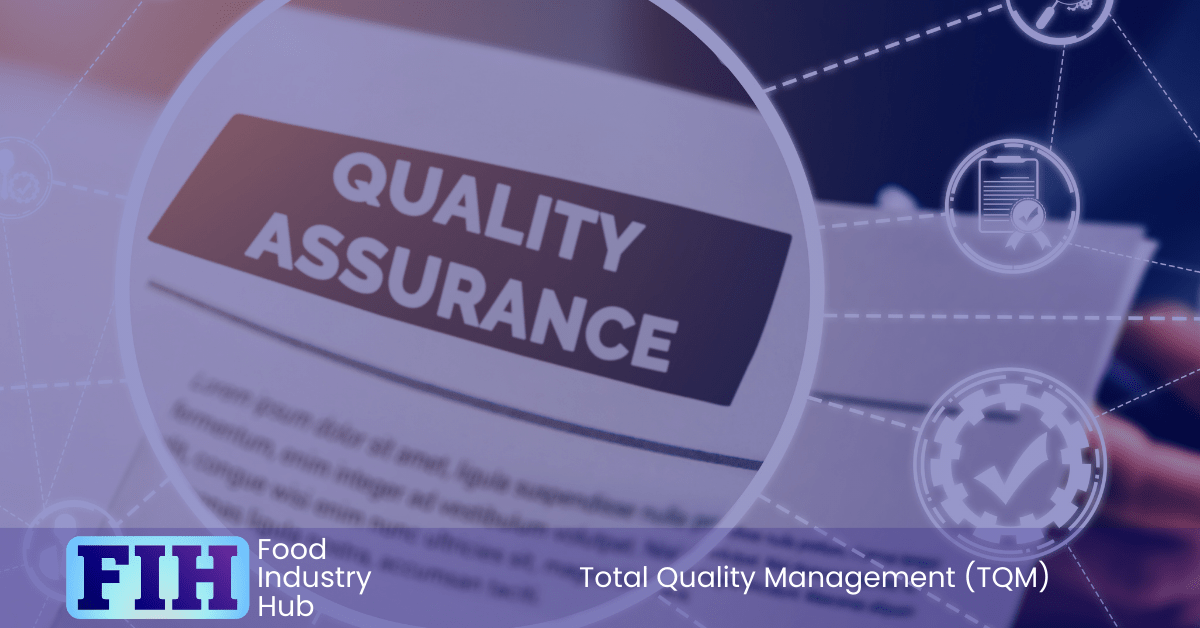
In Summary
Total Quality Management (TQM) is a crucial approach for food manufacturers to enhance quality, ensure safety standards, and drive efficiency.
By prioritising customer focus, fostering teamwork, effective communication, and continuous improvement, TQM implementation cultivates a culture of quality enhancement and collaboration within organisations.
Embracing TQM can lead to improved customer satisfaction, increased trust, and ongoing success in the competitive food manufacturing industry.
Further Resources
Food Industry Hub serves the food industry with a range of digital resources for the benefit of both commercial food manufacturers and food industry professionals.
For food manufacturers, we offer integrated management systems that give every user a direct interface with your QMS.
For food industry professionals, we provide an extensive signposting service in addition to informational content we hope you’ll find useful as you face new professional challenges. We have very ambitious plans to expand the range of services offered, and currently present informational content on management, safety and quality, food safety and quality culture, and professional success.