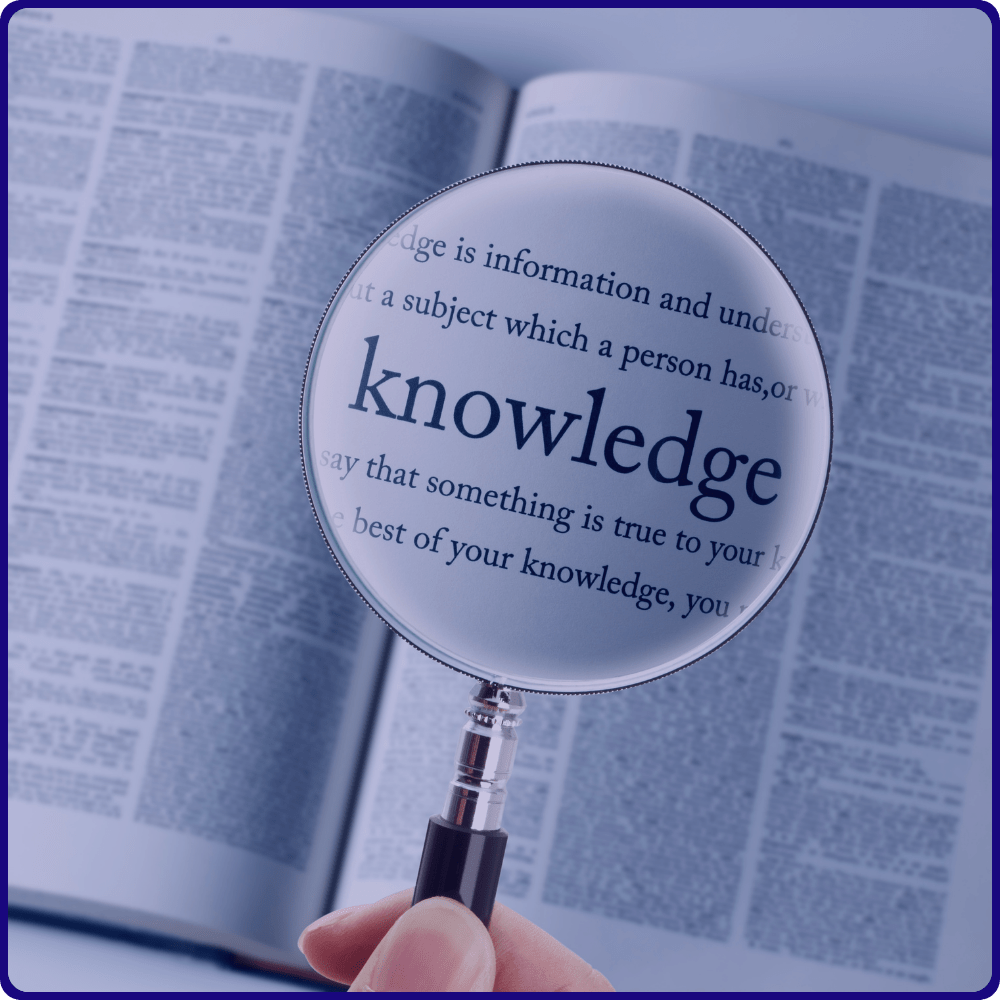
Sector-Specific Information
The Food Industry Hub knowledge centre delivers a wide range of sector-specific information for food industry professionals.
The below is one topic from our knowledge centre. You can return to all topics by clicking here.
Supplier Performance Monitoring and Supplier Scorecards
Introduction
Effective supplier performance monitoring is essential in maintaining quality, safety, and efficiency throughout the supply chain in food manufacturing. It involves tracking key performance metrics to evaluate and improve supplier relationships, ensuring that suppliers consistently meet contractual obligations, regulatory requirements, and quality standards. One common tool used to measure and communicate supplier performance is the supplier scorecard.
Importance of Supplier Performance Monitoring
- Ensuring Consistency:
- Monitoring supplier performance helps ensure that suppliers consistently meet agreed-upon standards, such as product quality, delivery timelines, and compliance with food safety regulations. It helps prevent any disruptions in the supply chain.
- Risk Mitigation:
- By tracking performance data, manufacturers can identify potential risks early, whether related to quality, delays, or non-compliance. This proactive approach allows businesses to take corrective actions before problems escalate.
- Continuous Improvement:
- Supplier performance monitoring supports continuous improvement. Suppliers that are regularly evaluated can receive feedback on their performance and identify areas for growth. This benefits both parties as it drives operational improvements.
- Cost Control:
- Effective monitoring helps manufacturers avoid unnecessary costs associated with poor supplier performance, such as production delays, product recalls, or additional quality checks. Identifying and addressing inefficiencies can help optimise costs across the supply chain.
- Regulatory Compliance:
- Continuous monitoring ensures suppliers adhere to regulatory requirements and food safety standards, reducing the risk of legal violations and ensuring product safety.
Key Metrics for Supplier Performance Monitoring
- Quality Metrics:
- Product Defects: Tracking the number of defective products delivered by the supplier.
- Conformance to Specifications: Ensuring that products meet predefined specifications (e.g., ingredient quality, packaging, labelling).
- Non-Conformance Rate: The frequency of non-compliance with quality standards or food safety and quality expectations.
- On-Time Delivery:
- Delivery Timeliness: Measuring the percentage of orders delivered on time.
- Lead Time Variability: Tracking fluctuations in lead time to help identify any patterns that may indicate delays.
- Cost Control:
- Price Competitiveness: Assessing whether the supplier’s prices are competitive compared to the market.
- Cost Consistency: Monitoring price changes and assessing whether they are in line with agreed terms.
- Customer Service and Responsiveness:
- Communication: Assessing how responsive and communicative the supplier is regarding orders, issues, or changes in requirements.
- Issue Resolution Time: Tracking how quickly the supplier resolves issues or complaints.
- Compliance:
- Standards Adherence: Ensuring that suppliers comply with all relevant food safety standards, such as HACCP, ISO 22000, and GSFI-recognised certifications.
- Audit Performance: Results from third-party audits or assessments of supplier facilities.
- Innovation and Continuous Improvement:
- Supplier Innovation: Evaluating the supplier’s ability to offer innovative solutions, new products, or improvements in quality or process.
- Supplier Development: The extent to which suppliers actively seek and implement continuous improvement initiatives.
- Sustainability and Ethical Practices:
- Environmental Impact: Evaluating the supplier’s environmental sustainability practices, such as waste reduction, energy efficiency, and sustainable sourcing.
- Ethical Sourcing: Ensuring suppliers adhere to ethical sourcing practices, such as fair labour standards and humane treatment of workers.
Supplier Scorecards
A supplier scorecard is a tool that summarises the key performance metrics and indicators for evaluating and rating supplier performance. It provides a comprehensive view of a supplier’s strengths, weaknesses, and overall reliability, enabling food manufacturers to make informed decisions about their supply chain.
Components of a Supplier Scorecard
- Scorecard Criteria:
- Quality: Product quality, defect rates, and conformance to specifications.
- Delivery: On-time delivery and lead time performance.
- Cost: Price competitiveness and cost stability.
- Service: Responsiveness to issues and customer service levels.
- Compliance: Adherence to regulatory standards and audit performance.
- Innovation: Contribution to product or process innovation.
- Sustainability: Environmental and ethical practices.
- Performance Rating:
- Each supplier is rated on each criterion, often using a numerical scale or color-coded system (e.g., red, yellow, green). This allows manufacturers to quickly identify areas of concern.
- Example: A score of 90% might indicate “exceeds expectations,” while 70% might indicate “meets expectations,” and below 70% could indicate “needs improvement.”
- Weighting of Criteria:
- Different criteria may be weighted differently based on their importance to the food manufacturing operation. For example, quality might have a higher weight than cost, as quality is crucial for ensuring food safety and meeting regulatory standards.
- Supplier Feedback:
- Include a section where suppliers can provide feedback on their performance. This can help foster collaboration and transparency and allow suppliers to address any areas of concern.
- Historical Data:
- Tracking performance over time can highlight trends, such as consistent issues with delivery or product quality. This data is valuable for decision-making and helps build long-term supplier relationships.
Steps for Implementing Supplier Performance Monitoring and Scorecards
- Define Performance Metrics:
- Identify the key metrics that align with your organisation’s goals and food safety requirements. These should be measurable, specific, and relevant to your supply chain.
- Set Clear Expectations:
- Establish clear expectations with suppliers regarding the performance metrics and how their performance will be evaluated. Ensure they understand the criteria for success.
- Track and Collect Data:
- Regularly track and collect performance data from suppliers. Use systems such as specialised supplier management software to automate the collection and tracking of data.
- Evaluate Performance:
- Periodically evaluate supplier performance using the scorecard. Make sure to analyse the data carefully to identify any trends or recurring issues that need to be addressed.
- Provide Feedback and Take Action:
- Share the scorecard results with suppliers and provide feedback on areas of improvement. Work with suppliers to create corrective actions for any issues and support them in improving their performance.
- Review and Adjust:
- Regularly review the supplier performance monitoring process and adjust as needed. As business goals or market conditions change, the criteria and weightings for supplier performance may need to be updated.
Best Practices for Supplier Performance Monitoring and Scorecards
- Collaborative Approach:
- Foster a cooperative relationship with suppliers rather than an adversarial one. Use scorecards as a tool for growth and improvement, not just for penalising poor performance.
- Continuous Communication:
- Maintain regular communication with suppliers to keep them informed of performance expectations and changes. Transparency helps build trust and improve the relationship.
- Actionable Data:
- Ensure the data collected is actionable. Don’t just measure performance—use it to inform decisions, drive improvements, and address concerns.
- Focus on Long-Term Partnerships:
- While performance monitoring is important, aim for long-term relationships with suppliers. Use scorecards as part of a strategy to continuously improve the supply chain, rather than to simply evaluate short-term performance.
- Incorporate Technology:
- Leverage technology, such as supply chain management software, to streamline the process of performance monitoring and improve data collection, analysis, and reporting.
Conclusion
Supplier performance monitoring and scorecards are essential tools for ensuring food manufacturers maintain a high standard of quality, compliance, and efficiency throughout the supply chain. By regularly assessing supplier performance against predefined criteria, manufacturers can identify opportunities for improvement, manage risks, and foster strong, collaborative relationships with suppliers. Implementing a robust supplier assurance program that includes monitoring and scorecards not only enhances product quality and safety but also supports the long-term sustainability of the business.
Food Industry Hub Management Systems provides a comprehensive digital solution for food safety and quality management, helping you to stay compliant and audit-ready.
About The Food Industry Hub Knowledge Centre
The Food Industry Hub knowledge centre delivers informative content on a variety of topics pertinent to the food manufacturing industry.
You can return to all topics by clicking here.
We regularly produce new content for food industry professionals, and the Food Industry Hub Mail Service is the best way to stay up to date with the latest additions.
Signup today to be added to the Food Industry Hub mailing list.