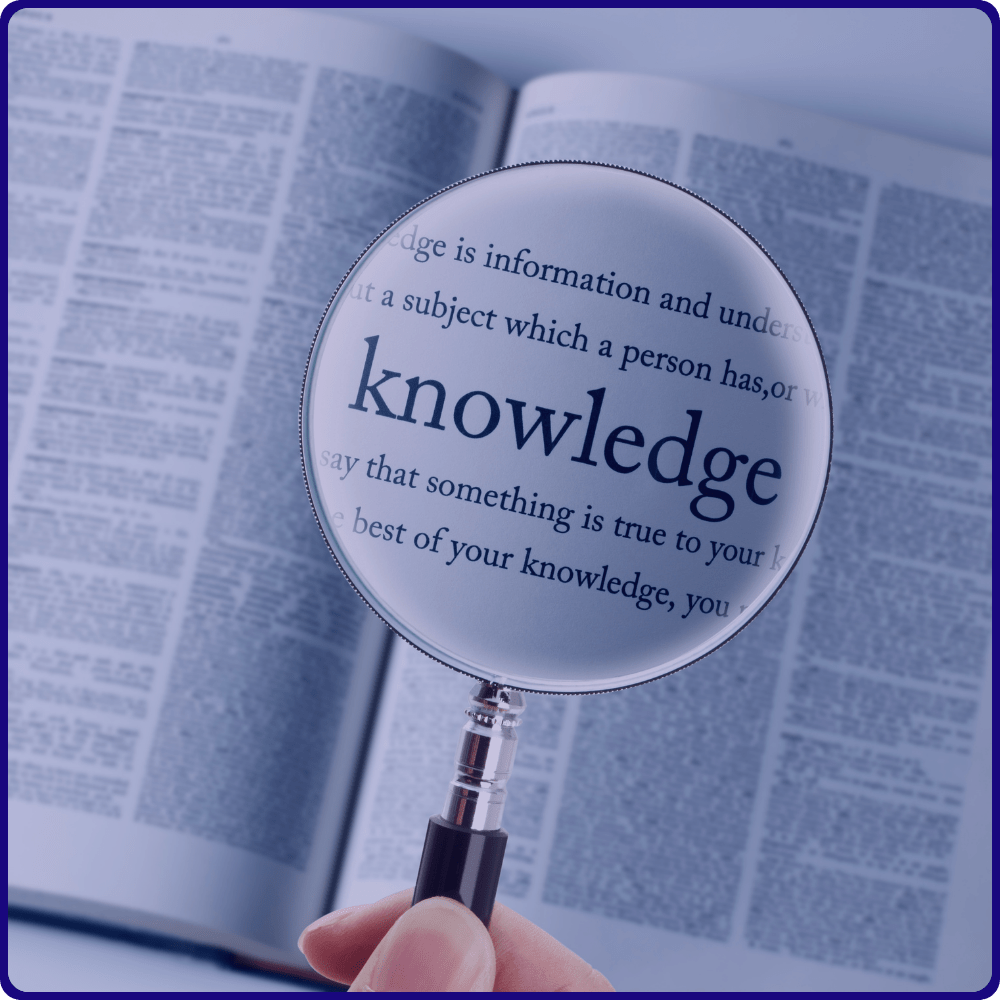
Sector-Specific Information
The Food Industry Hub knowledge centre delivers a wide range of sector-specific information for food industry professionals.
The below is one topic from our knowledge centre. You can return to all topics by clicking here.
Product Recall and Withdrawal
Introduction
Product recall and product withdrawal are important responsive processes in the food manufacturing industry aimed at protecting public health and ensuring consumer safety. Both actions are taken in response to identified food safety risks or quality issues, but they differ in their scope, trigger points, and regulatory requirements.
Product Recall
A product recall refers to the action taken by a food manufacturer or distributor to remove a product from the market or consumer use because it poses a health risk or fails to meet safety standards. Recalls are typically initiated when an unsafe or non-complianct product has been distributed to consumers, retail outlets, or food service establishments.
Reasons for Product Recall
- Contamination: Presence of harmful pathogens (e.g., Salmonella, E. coli, Listeria) or foreign objects (e.g., glass, metal).
- Ingredient Mislabelling: Incorrect allergen declarations, missing nutritional information, or inaccurate ingredient lists.
- Product Misbranding: Errors in labelling regarding origin, quantity, or packaging that may mislead consumers or violate food labelling regulations.
- Regulatory Non-Compliance: Failure to meet national or international food safety or quality regulations (e.g., exceeding pesticide limits, improper storage conditions).
Recall Process
The recall process generally involves several stages:
- Detection: Identifying that a product is unsafe or non-compliant. This can be triggered by customer complaints, laboratory testing, surveillance, or regulatory inspection. The scope or extent of the product batch(es) affected must be determined, as well as forward distribution (traceability).
- Notification: The manufacturer or regulatory authority notifies stakeholders, including consumers, retailers, and distributors. Public warnings may be issued through websites, press releases, or government channels.
- Removal: Products are removed from store shelves, warehouses, and distribution networks. Affected products are returned or destroyed to prevent further consumer exposure.
- Investigation: The cause of the issue is investigated, such as the source of contamination, faulty manufacturing processes, or labeling errors.
- Corrective Actions: Steps are taken to correct the identified issue and prevent recurrence, which may include process changes, additional quality controls, or supplier audits.
- Reimbursement/Replacement: Depending on the nature of the recall, affected consumers may be offered a refund, replacement product, or compensation.
Regulatory Requirements for Recalls
- Food Standards Authority: In many countries, food safety authorities (e.g., the Food Standards Agency in the UK, the U.S. FDA) have established guidelines and reporting requirements for recalls.
- Traceability: Manufacturers must maintain product traceability systems to ensure affected products can be identified and removed efficiently.
Product Withdrawal
A product withdrawal occurs when a product is removed from the market, but it is not necessarily recalled from consumers. Unlike a recall, a withdrawal typically involves removing products that do not meet quality standards, consumer preference, or other non-safety-related issues.
Reasons for Product Withdrawal
- Quality Issues: Substandard taste, texture, or appearance that does not meet brand or consumer expectations.
- Non-Compliance with Specifications: Minor deviations from product specifications that do not pose a safety risk but may affect product quality.
- Labeling Errors: Minor inaccuracies in the label which do not pose a safety risk but require correction.
- Supply Chain or Distribution Problems: Disruptions in the supply chain, including transportation issues or distribution errors, that lead to products being pulled from the market before they reach consumers.
- Business Decision: The manufacturer may choose to withdraw a product due to low sales, a change in production plans, or a marketing strategy shift.
Withdrawal Process
- Decision to Withdraw: The company identifies that a product does not meet its quality or branding standards. This could be due to consumer complaints, internal quality assurance tests, or issues flagged by retailers.
- Notification: The company informs distributors, retailers, and other stakeholders, but the withdrawal does not necessarily involve public notification or a public health alert.
- Removal: The product is removed from store shelves and distribution networks. It is typically replaced with an updated or improved version of the product.
- Investigation and Resolution: The company investigates why the product did not meet expectations and takes corrective actions, which may include reformulation, process adjustments, or new quality assurance checks.
Regulatory Requirements for Withdrawals
While withdrawals may not require formal reporting to regulatory authorities unless they involve a significant safety risk, manufacturers still need to follow industry standards and internal procedures to ensure that the withdrawal is handled properly. In some cases, public notification may still be required if the withdrawal concerns a product that is widely distributed.
Key Differences Between Product Recall and Withdrawal
Aspect | Product Recall | Product Withdrawal |
Trigger | Safety risk, contamination, mislabelling, non-compliance | Quality issues, consumer preference |
Scope | Involves removing products from consumer use due to safety concerns | Involves removing products from the market due to non-safety issues like quality |
Public Notification | Often involves public warning or press release | Typically does not require public notification unless safety is impacted |
Regulatory Reporting | Mandatory in most jurisdictions for safety-related issues | Not typically required unless public safety is involved |
Impact on Consumer Health | Potential health risk to consumers | No significant health risk to consumers |
Examples | Contaminated food products, mislabelling of allergens | Substandard quality, packaging errors, supply chain issues |
Best Practices for Product Recall and Withdrawal
- Establish a Recall / Withdrawal Plan: Develop a detailed recall strategy that includes procedures for identifying, isolating, and removing affected products from the market quickly.
- Maintain Traceability Systems: Ensure robust traceability of raw materials, production batches, and distribution channels to enable fast identification of affected products.
- Training: Regularly train staff on recall and withdrawal procedures to ensure that everyone knows their roles and responsibilities during an emergency.
- Rapid Communication: Ensure clear and effective communication with customers, suppliers, and regulatory bodies. This can help mitigate the risk of brand damage and consumer harm.
- Documentation: Keep accurate records of recalls and withdrawals for compliance and future audits.
- Consumer Compensation: Provide appropriate compensation or replacement products to affected consumers to mitigate damage to brand trust and customer loyalty.
Conclusion
Both product recalls and withdrawals play vital roles in ensuring food safety and quality. While recalls are essential to address health risks and regulatory non-compliance, withdrawals are more commonly associated with maintaining brand integrity and addressing minor issues without public health consequences. Properly managing these processes ensures that manufacturers maintain consumer trust, comply with regulations, and safeguard public health.
Manage quality assurance and food safety compliance effectively with Food Industry Hub Management Systems.
About The Food Industry Hub Knowledge Centre
The Food Industry Hub knowledge centre delivers informative content on a variety of topics pertinent to the food manufacturing industry.
You can return to all topics by clicking here.
We regularly produce new content for food industry professionals, and the Food Industry Hub Mail Service is the best way to stay up to date with the latest additions.
Signup today to be added to the Food Industry Hub mailing list.