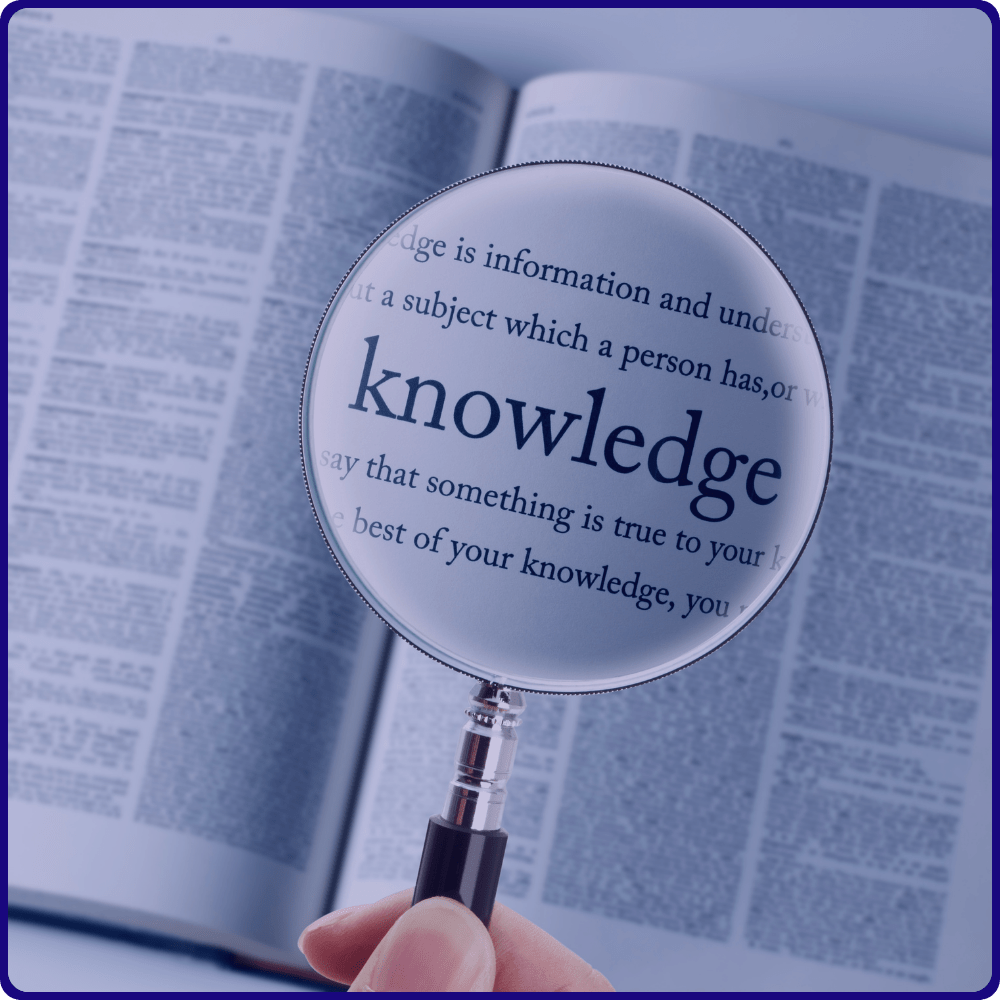
Sector-Specific Information
The Food Industry Hub knowledge centre delivers a wide range of sector-specific information for food industry professionals.
The below is one topic from our knowledge centre. You can return to all topics by clicking here.
Capacity Planning in Food Processing Operations
Definition
Capacity planning in food processing operations is the systematic approach to determining the production capacity required to meet fluctuating demands. It encompasses analysing current production capabilities, forecasting demand, and adjusting resources to ensure efficient operations, cost-effectiveness, and adherence to quality and safety standards. In the food manufacturing industry, capacity planning is pivotal in synchronising resources, mitigating waste, and aligning with both regulatory requirements and customer expectations.
Food processing plants are intricate systems, integrating raw material handling, processing, packaging, and distribution. Effective capacity planning ensures each stage has sufficient resources, such as equipment, labour, and materials, to fulfil production objectives. It also accounts for constraints like facility size, equipment performance, labour availability, and financial budgets, striving to balance production throughput with operational limits.
Practical Applications
Demand Forecasting
Accurate demand forecasting underpins effective capacity planning. This involves analysing historical sales data, seasonal trends, promotional activity, and market dynamics to predict future product requirements. For instance, a manufacturer of ready-to-eat meals might see increased demand during holiday seasons. Robust forecasting helps determine the production scale needed, avoiding overproduction or shortages.
Evaluating Current Capacity
Once demand forecasts are established, manufacturers assess their current capacity by evaluating machinery, labour, and storage. For example, a bakery anticipating higher sales of festive cakes might identify gaps in its current mixing or baking capacity. Addressing these gaps could involve leasing equipment or introducing an additional production shift.
Optimising Capacity Utilisation
Capacity utilisation measures how efficiently production resources are used. While high utilisation can indicate efficiency, overuse risks machinery wear and compromised product quality. A beverage producer might achieve balanced utilisation by rotating production lines for downtime and maintenance, ensuring smooth operations.
Addressing Bottlenecks
A bottleneck is a production constraint that hampers output. For example, in a jam production line, a slower filling station might delay the packaging process. Addressing such bottlenecks could involve upgrading equipment or redistributing labour.
Adjusting for Seasonality
Seasonal fluctuations are common in food manufacturing. Ice cream producers, for instance, face peak demand in summer. During such periods, additional capacity can be achieved by hiring temporary workers, leasing cold storage, or running additional shifts.
Scenario Planning and Flexibility
Unexpected situations, such as supply chain disruptions or equipment failures, require contingency plans. A snack manufacturer might develop alternative sourcing strategies for key ingredients like potatoes or oil to mitigate risks and maintain operations.
Regulatory Considerations
Capacity planning in food processing must align with stringent UK and EU regulations. For instance:
- Food Safety Standards: The capacity planning process must consider hygiene and food safety guidelines under regulations like the UK Food Safety Act 1990 or EU Regulation (EC) No 852/2004. Adequate capacity must account for compliance, such as maintaining separate lines for allergen-containing products.
- Environmental Sustainability: Under EU sustainability goals, manufacturers are incentivised to optimise energy use and minimise waste. For example, adopting energy-efficient machinery can help meet these standards while reducing operational costs.
- Workforce Regulations: Labour planning must adhere to the Working Time Regulations 1998 (UK), ensuring compliance with laws on shifts, rest periods, and overtime.
Significance for Product Quality and Safety
Capacity planning directly impacts product quality and safety. Inefficient processes or overburdened equipment can compromise quality. For instance, insufficient cooling capacity in a dairy plant may result in inadequate chilling, risking bacterial growth. Planning for redundancies, such as backup refrigeration systems, mitigates these risks.
Expert Insights
Automation and Smart Manufacturing
Automation enhances capacity planning by improving precision and efficiency. Automated systems can monitor equipment utilisation, predict maintenance needs, and dynamically adjust production rates. A confectionery manufacturer, for example, could use smart sensors to ensure uniform chocolate coating, optimising line speeds and minimising waste.
Sustainability and Capacity
Sustainability is intertwined with capacity planning. Manufacturers are adopting strategies such as waste reduction and energy optimisation. A poultry processor, for example, might invest in water recycling systems to improve environmental outcomes while ensuring compliance with sustainability certifications.
Related Concepts
Effective inventory management ensures raw materials and packaging are available without overstocking. For instance, just-in-time (JIT) inventory systems align deliveries with production schedules, reducing storage costs and spoilage risks.
Maintenance and Equipment Reliability
Regular maintenance minimises downtime and enhances reliability. A brewery, for example, could implement a predictive maintenance program to reduce unplanned breakdowns, ensuring consistent capacity.
Labour Planning
Labour shortages can impact capacity. Workforce planning involves not only staffing levels but also training for specialised roles. A cheese manufacturer may need skilled operators for ageing and slicing processes to maintain quality and meet production targets.
Conclusion
Effective capacity planning ensures food manufacturers can meet current and future demand while optimising costs, maintaining quality, and adhering to safety and regulatory standards. By leveraging advanced technologies, fostering sustainability, and addressing operational constraints, food processing plants can achieve operational excellence and remain agile in dynamic market conditions.
Food Industry Hub Management Systems can significantly boost the effectiveness of your food safety and quality management system, leading to improved confidence and elevated quality assurance throughout your operations.
About The Food Industry Hub Knowledge Centre
The Food Industry Hub knowledge centre delivers informative content on a variety of topics pertinent to the food manufacturing industry.
You can return to all topics by clicking here.
We regularly produce new content for food industry professionals, and the Food Industry Hub Mail Service is the best way to stay up to date with the latest additions.
Signup today to be added to the Food Industry Hub mailing list.